DJ Nelson
Aerospace
- Oct 2, 2023
- 7
We have a step pin the tolerancing seems to be incorrect.
See Datum A on the Attachment they call out total run out of .0015 on datum A.
in sec 9.2 one part in the standard that resembles our pin we have it seems as if you can not applied Total runout to the datum.
In sec 9.4 the standard it gives another example were if you have multiple datums a significant length or axis separation.
We think they should maybe change the call out to either straightness or cylindricity.
See Datum A on the Attachment they call out total run out of .0015 on datum A.
in sec 9.2 one part in the standard that resembles our pin we have it seems as if you can not applied Total runout to the datum.
In sec 9.4 the standard it gives another example were if you have multiple datums a significant length or axis separation.
We think they should maybe change the call out to either straightness or cylindricity.
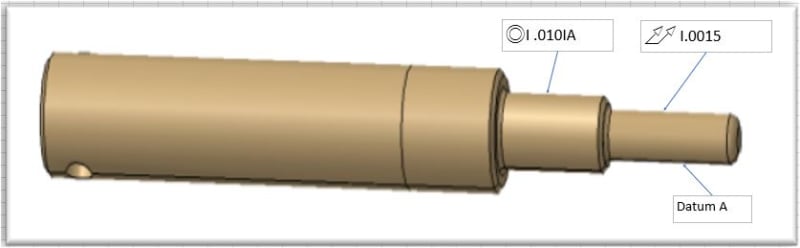