Rwelch9
Mechanical
- Apr 22, 2020
- 116
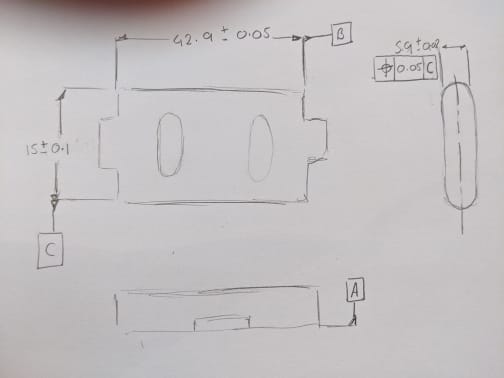
Hi ,
I have a couple of queries about the sketch i did .
Datum feature C would this be a derived line between the two axis of the radii at each end of the component
The True position call out ± 0.05 to Datum feature C , is this a valid call out ?
Thanks
R