ASHWA
Automotive
- Oct 7, 2020
- 53
Hi Friends,
Need a help in reg. Two Datum Features, Single Datum Axis.
Is my assumption correct?
Thanks.
Need a help in reg. Two Datum Features, Single Datum Axis.
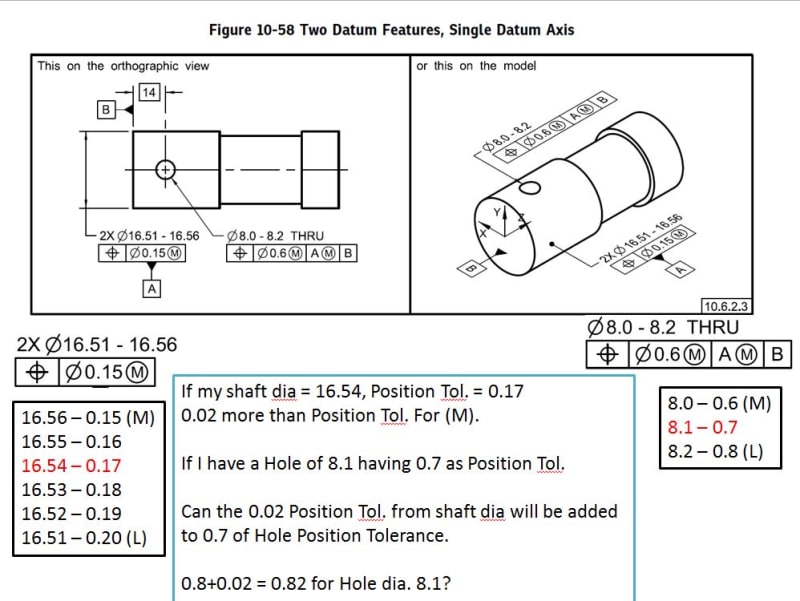
Is my assumption correct?
Thanks.