Hi everyone,
I was checking a dwg and got confused with how a datum displacement should work a position tolerance:
If I understood correctly the MMC modifier of the center position of the eccentric cylinder, it means it can vary within a circle of 0.008mm when the diameter is maximum (24.2291mm) and will be expanded to 0,0207mm when it is in its minimum allowed value (24.2164mm), correct?
How about the MMC modifier to the A datum? I could not understand how the datum displacement would apply in this case.
Thanks for your help,
I was checking a dwg and got confused with how a datum displacement should work a position tolerance:
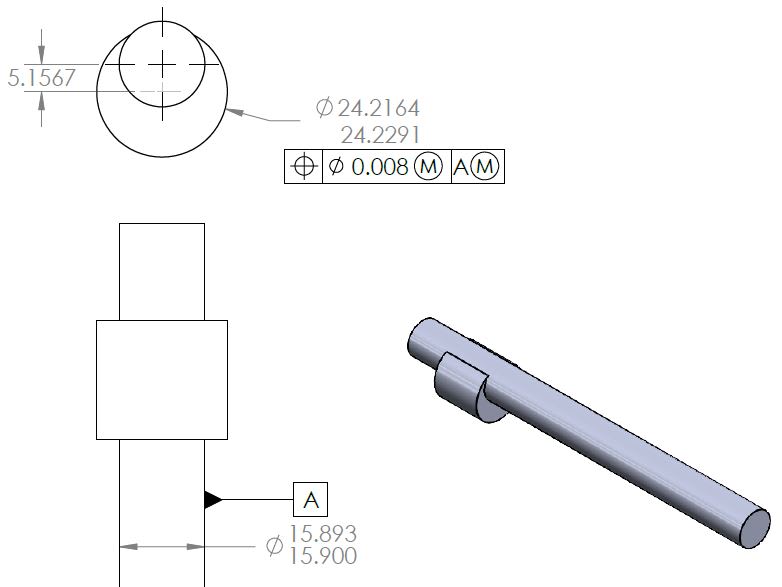
If I understood correctly the MMC modifier of the center position of the eccentric cylinder, it means it can vary within a circle of 0.008mm when the diameter is maximum (24.2291mm) and will be expanded to 0,0207mm when it is in its minimum allowed value (24.2164mm), correct?
How about the MMC modifier to the A datum? I could not understand how the datum displacement would apply in this case.
Thanks for your help,