DRWCA
Mechanical
- May 14, 2020
- 2
Curious about the interpretation of the unilateral tolerance zone in the following example. As A departs from MMC, does the bonus tolerance applied to the profile control now allow for removal of material, or is the implied 'outside only' condition preserved, ie. would the implied profile callout at a diameter of 14.8 be |0.5 U 0.1| or |0.5 U 0.5|?
Or perhaps the better question - is this even a valid callout?
Or perhaps the better question - is this even a valid callout?
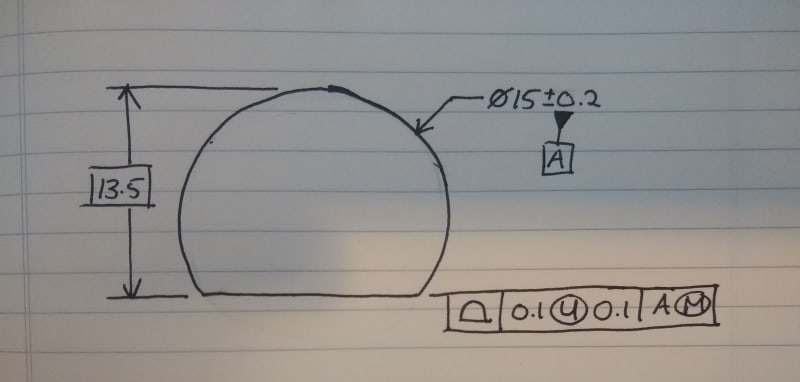