PrintScaffold
Mechanical
Very impressive! Does anybody know which CAD did they use? Was it NX, CATIA, or something else?
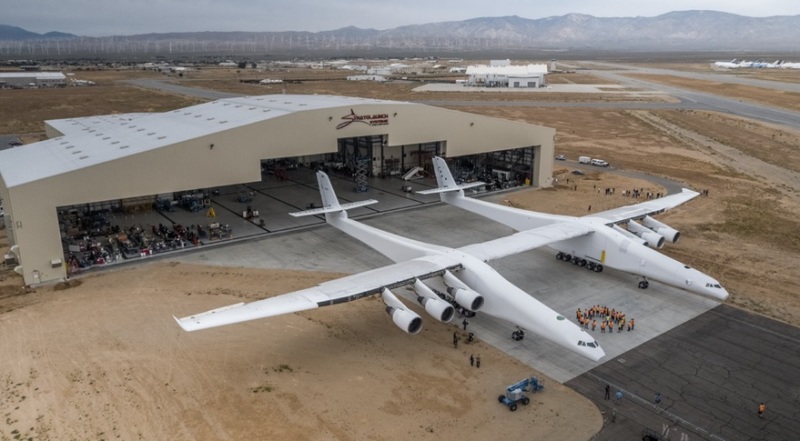
Follow along with the video below to see how to install our site as a web app on your home screen.
Note: This feature may not be available in some browsers.
JNieman said:Solidworks and other "middle of the road" CAD packages have come a long way since I last worked with them several years back. They have been incorporating a lot more freeform surfacing tools, flow and thermal analysis, and some FEA tools. I have not used any such tools. I was just surprised to learn of it. It's possibly just something that makes 'pretty pictures' that will make minor/less-critical design work "look better" or make pretty pictures for advertising materials that make them look like a more advanced/competent engineering team... or maybe it's pretty legit. I dunno. The people I know using Solidworks use more established CAE tools.
PrintScaffold said:There were some interesting comments suggesting inexperience of the designers. A honest question (I do not live in US) - is it possible in US that someone inexperienced is hired to do such kind of job? If yes, what is the reason? Is it because all experienced aerospace designers would not want to leave their good jobs for some dodgy startup or what?
This aircraft bears NONE of the characteristics of a Burt Rutan design.
SparWeb said:This aircraft bears NONE of the characteristics of a Burt Rutan design.