BendingMoment123
Structural
Hi, I just want to verify my stress results in my plate segments in Strand7 using Roark's formula. Should I use the surface (either -Z or +Z in terms of the plate's local axes. In this case the top of the plate is the -Z surface), or mid surface calculated stresses. So you would have either a mid surface stress in the global xx,yy and zz directions, and you would have -Z surface stress calculated in the global xx, yy and zz directions.
Note that the dark green plates are stiffeners welded to the surface of the light green plate. I just want to check a portion of the light green plate, which I have highlighted in red below. The highlighted portion has a uniform pressure applied over it of 7300 kPa. The plate dimensions are 2" X 2" (50.8 mm X 50.8 mm) and is 17.5 mm thick. What edge support configuration would you assume as well?
Note that the dark green plates are stiffeners welded to the surface of the light green plate. I just want to check a portion of the light green plate, which I have highlighted in red below. The highlighted portion has a uniform pressure applied over it of 7300 kPa. The plate dimensions are 2" X 2" (50.8 mm X 50.8 mm) and is 17.5 mm thick. What edge support configuration would you assume as well?
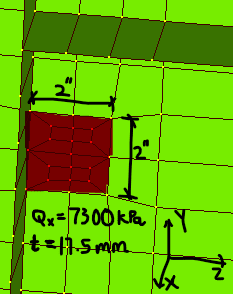