MechvsManu
Mechanical
- Mar 20, 2024
- 24
This is a lifter I have designed to lift 1000lbs. This is one side and is mirrored on the other side. The cylinder is capable of 700lbs.
Will the cylinder being off and not centered between the linear shafts/bearings have an issue with lifting?
Also would it help if I did 2 cylinders in the location of the red arrows over one larger cylinder in the center? Or would that cause a binding issue?
I'm clamping against an upper frame so I don't need the cylinders to lift exactly simultaneously.
I don't have space to mount the cylinder under and centered due to clearance issues.
Will the cylinder being off and not centered between the linear shafts/bearings have an issue with lifting?
Also would it help if I did 2 cylinders in the location of the red arrows over one larger cylinder in the center? Or would that cause a binding issue?
I'm clamping against an upper frame so I don't need the cylinders to lift exactly simultaneously.
I don't have space to mount the cylinder under and centered due to clearance issues.
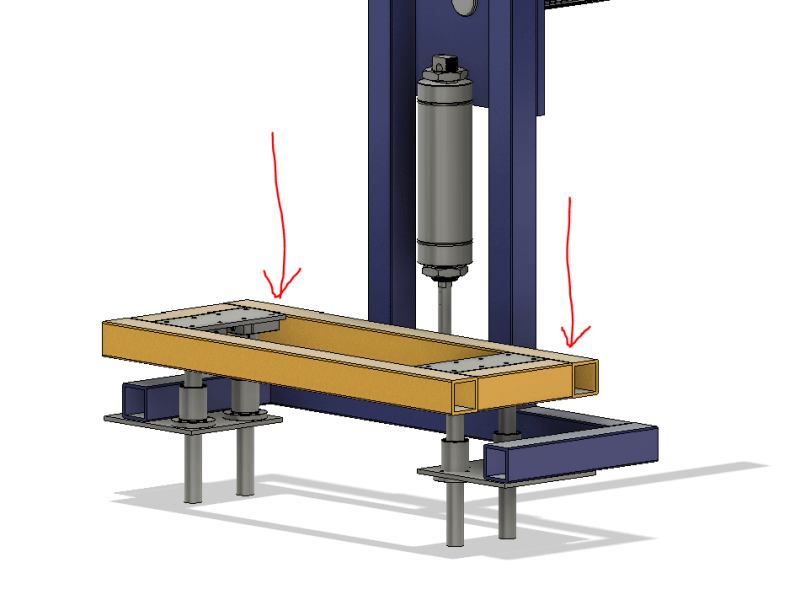