dawz
Mechanical
- Feb 26, 2024
- 23
we have a 3 B-Type V-belt tensioner for engine with a spring pulling the tensioner roller. The spring is then connected to a stud/hook through the cabin and wing nut is used to pull up the spring to increase the belt tension. 2 wing nuts are used, one on top of console and one at the bottom of console.
Wing nut with spring washer and common washer:
Recently we had a case of loose wing nut and causing damage to thread stud. I have thought of many ways to make it not loose, among them are pvc washers, spring washers, curved washers, Nord locks. I'm sure nord-locks aren't suitable for this application due to belt requiring adjustment after operating for some time. The criteria is not to use spanner to fasten.
the damaged thread:
I had an idea of making a collar to prevent thread contact with metal sheet, but this requires a spanner.
background: Wing nut was used because there was a complain about the v-belt coming loose and operators in the plantation are unable to adjust the belt due to a lack of spanner. So wing nut was selected due to convenience in adjusting belt tension.
I'm sure this invites a lot of criticisms and ideas because, belt tensioning and hand turning doesn't go hand in hand. If you have a better idea, I would love to hear.
For now, belt tensioner was fastened with wing nut, spring washer and common washer with a spanner. But I don't have a convincing enough reason to the team as to why we need to use spanner to fasten the stud other than to prevent loosening/vibration damage to the stud.
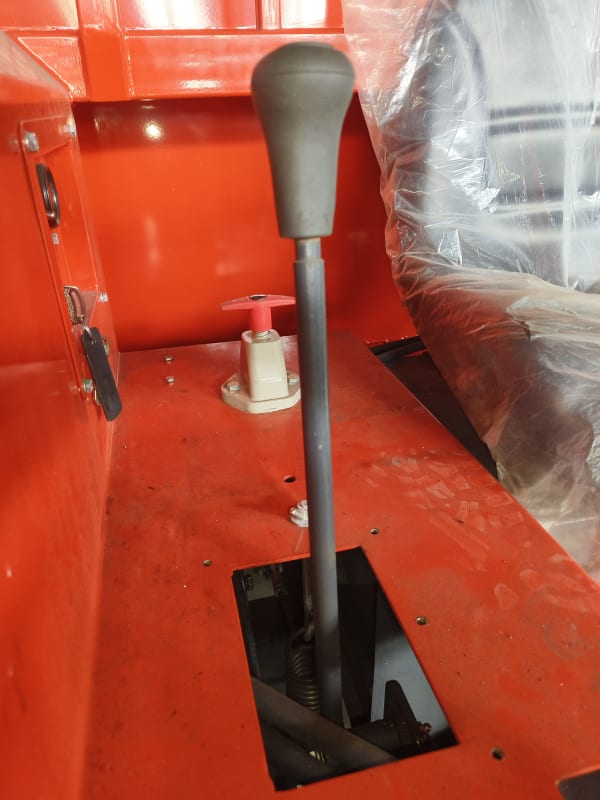
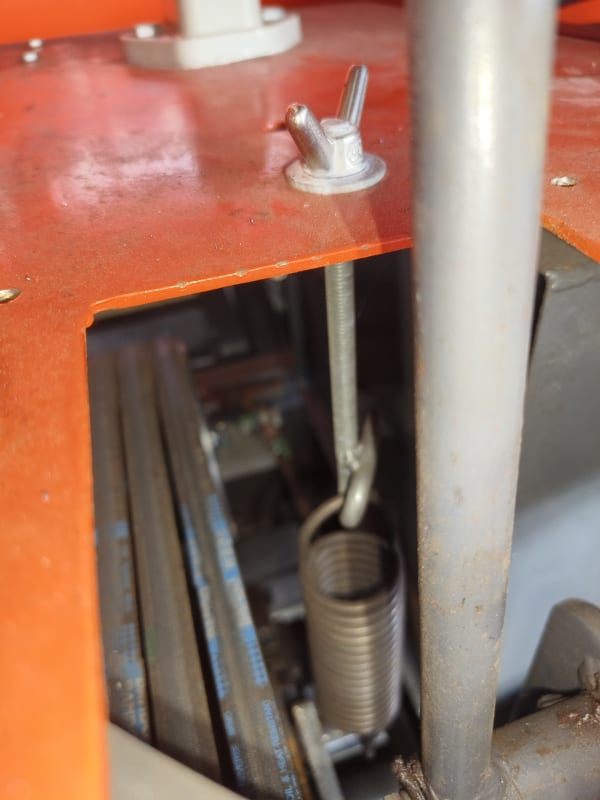
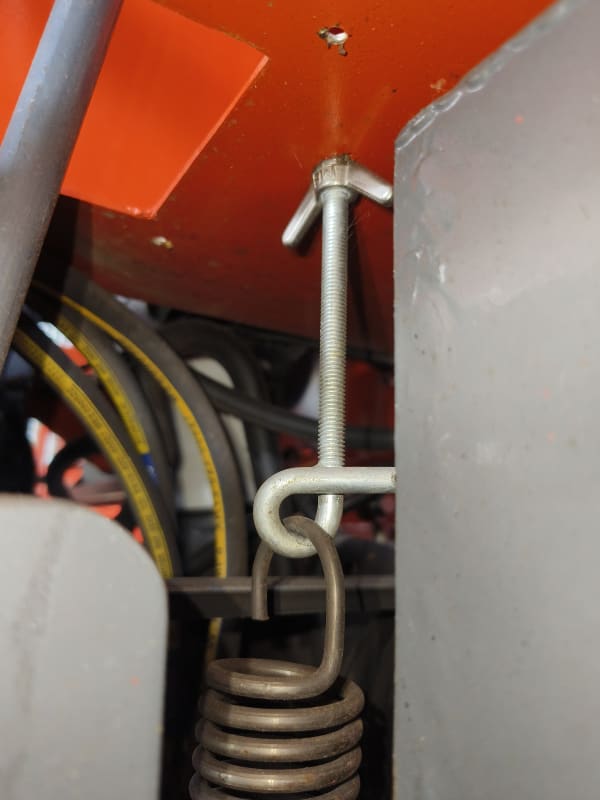
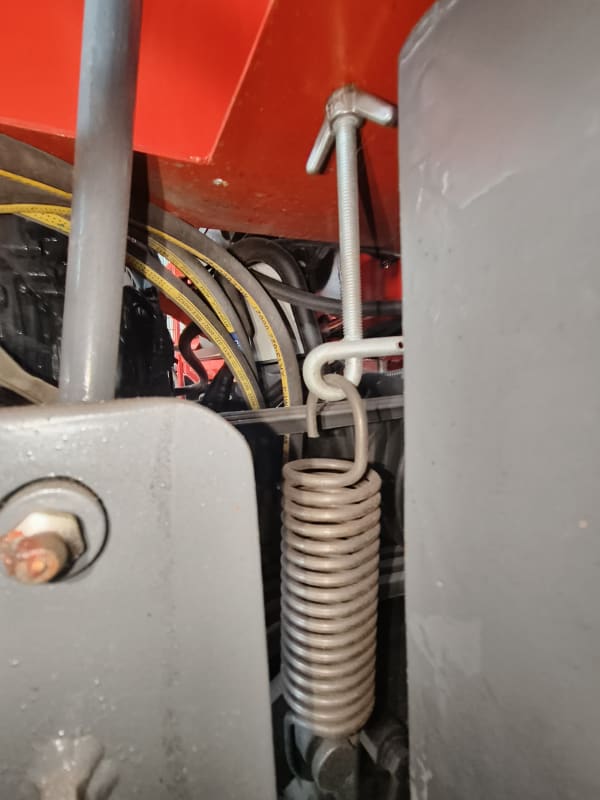
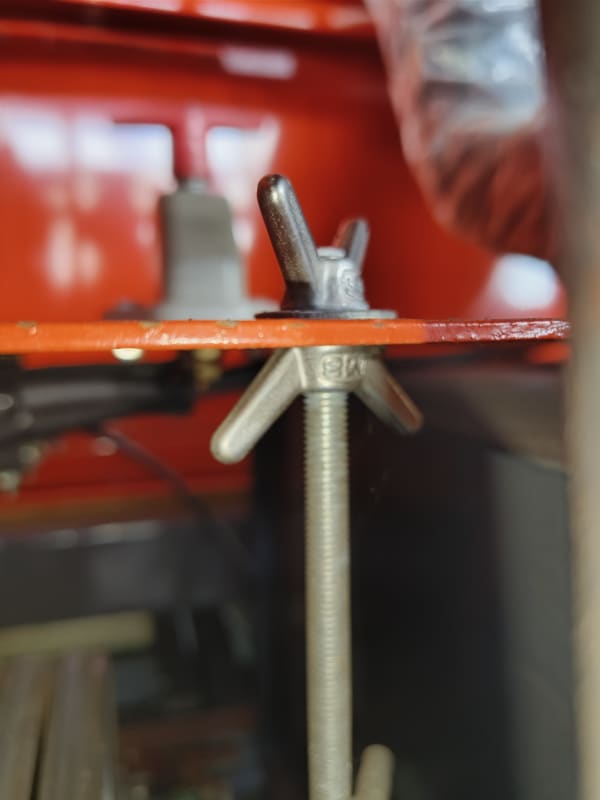
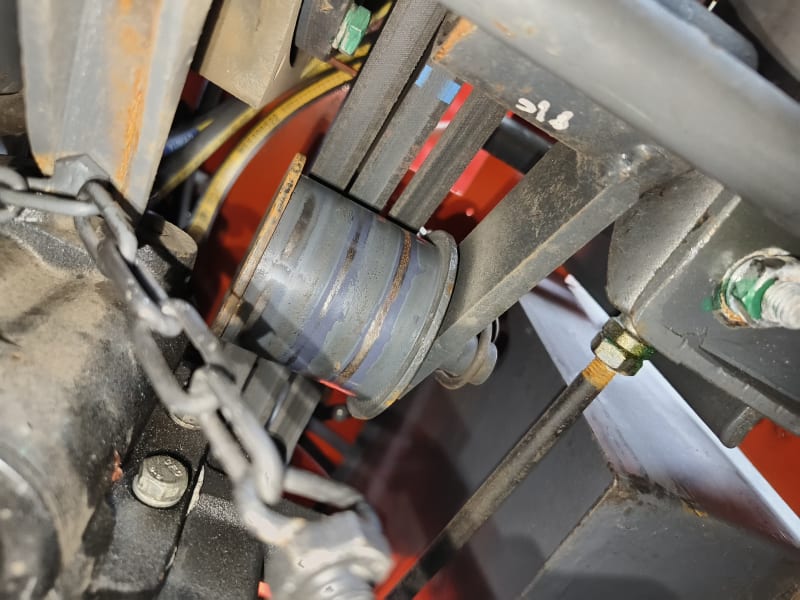
Wing nut with spring washer and common washer:
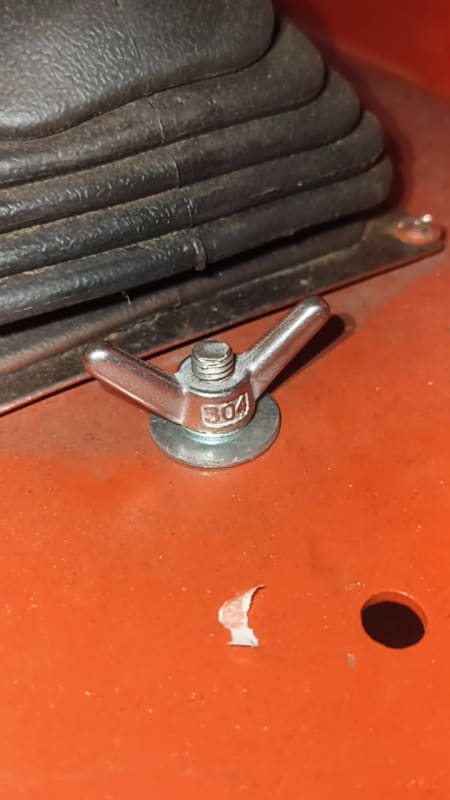

Recently we had a case of loose wing nut and causing damage to thread stud. I have thought of many ways to make it not loose, among them are pvc washers, spring washers, curved washers, Nord locks. I'm sure nord-locks aren't suitable for this application due to belt requiring adjustment after operating for some time. The criteria is not to use spanner to fasten.
the damaged thread:
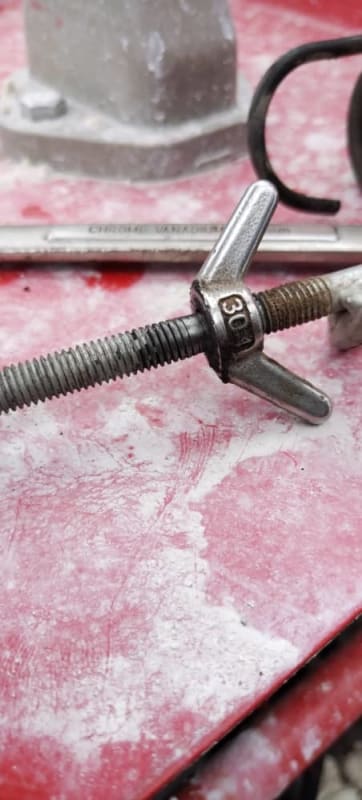
I had an idea of making a collar to prevent thread contact with metal sheet, but this requires a spanner.
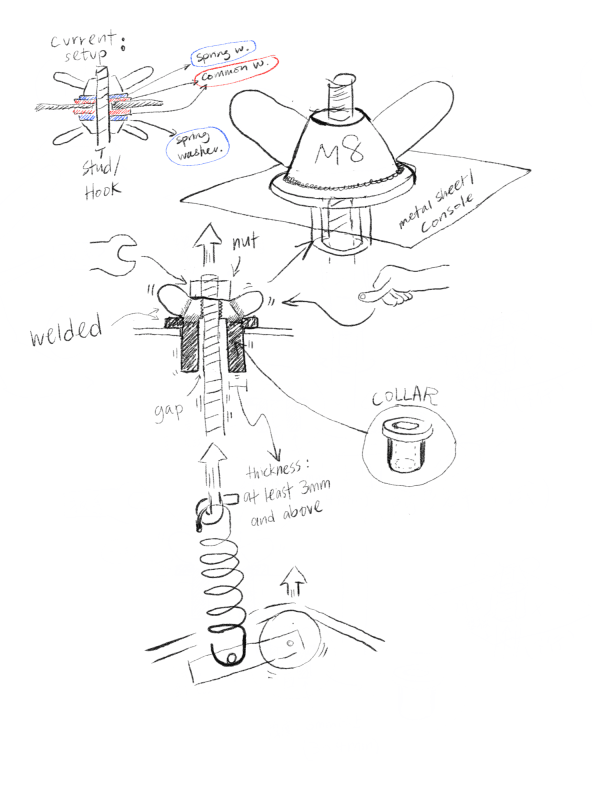
background: Wing nut was used because there was a complain about the v-belt coming loose and operators in the plantation are unable to adjust the belt due to a lack of spanner. So wing nut was selected due to convenience in adjusting belt tension.
I'm sure this invites a lot of criticisms and ideas because, belt tensioning and hand turning doesn't go hand in hand. If you have a better idea, I would love to hear.
For now, belt tensioner was fastened with wing nut, spring washer and common washer with a spanner. But I don't have a convincing enough reason to the team as to why we need to use spanner to fasten the stud other than to prevent loosening/vibration damage to the stud.