Hello,
Been a while since I posted here. I've got a situation where I need to apply a position tolerance to the centerplane of a dovetail slot.
Since the dovetail slot is a complex shape and the functional part is tapered, I think that the centerplane of the slot is not entirely clear. So, I propose that I could use datum targets to establish the centerplane, and apply the position tolerance to the datum plane (see the note "APPLIES TO DATUM S" below). But, I wonder if that is clear?
I've made a simplified sketch of what I'm working with, and I wonder if there is a better way to accomplish it?
Thoughts?
-Chris
Been a while since I posted here. I've got a situation where I need to apply a position tolerance to the centerplane of a dovetail slot.
Since the dovetail slot is a complex shape and the functional part is tapered, I think that the centerplane of the slot is not entirely clear. So, I propose that I could use datum targets to establish the centerplane, and apply the position tolerance to the datum plane (see the note "APPLIES TO DATUM S" below). But, I wonder if that is clear?
I've made a simplified sketch of what I'm working with, and I wonder if there is a better way to accomplish it?
Thoughts?
-Chris
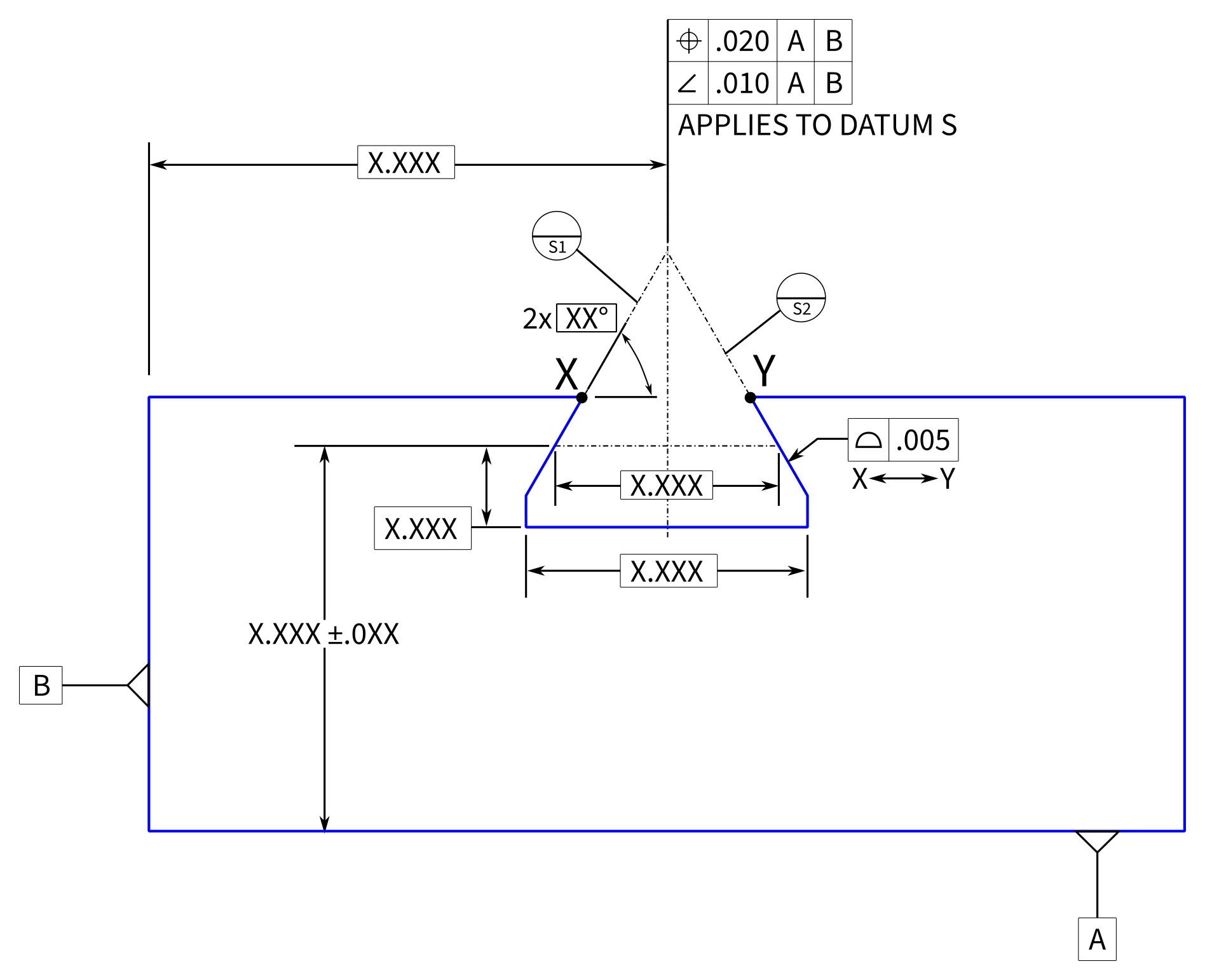