TugboatEng
Marine/Ocean
Background: I have an engine that I've received into my fleet that smokes at full power. These engines are essentially new and confirmed to be in good operating condition by the manufacturer. Everybody else's stumped so I get to take my turn at it.
What I have found is that the engine is installed very close to the after bulkhead of the engine room and the air filter box was modified to fit in this space. During the modification, the radiused inlet to the turbocharger was removed to space constraints. It is my belief that the squared off entry is choking the turbocharger for air.
Now I need to figure out how to correct this issue with limited space. I thought about projecting the inlet pipe into the air box and flaring the end of it. Much like a velocity stack on an old carburetor.
However, this reentrant geometry may also provide the worst k factor.
What I have found is that the engine is installed very close to the after bulkhead of the engine room and the air filter box was modified to fit in this space. During the modification, the radiused inlet to the turbocharger was removed to space constraints. It is my belief that the squared off entry is choking the turbocharger for air.
Now I need to figure out how to correct this issue with limited space. I thought about projecting the inlet pipe into the air box and flaring the end of it. Much like a velocity stack on an old carburetor.
However, this reentrant geometry may also provide the worst k factor.
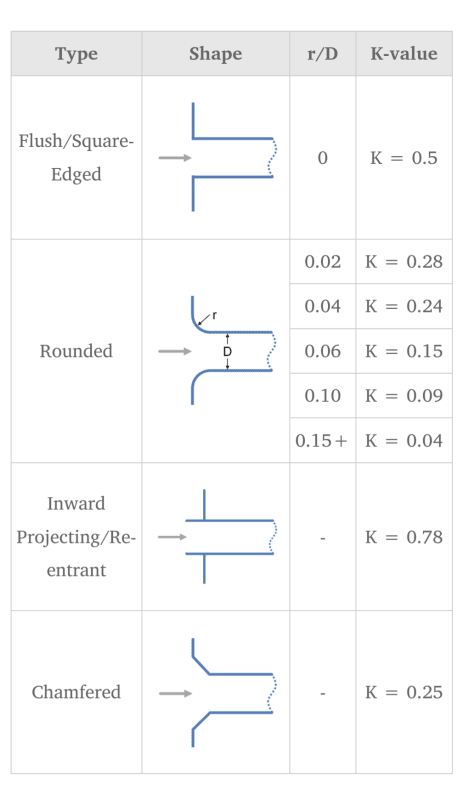