AlexFH
Mechanical
- Apr 29, 2024
- 3
Hi,
In this case, Datum B is a group of four faces. Should I use B or B-B?
I have always used B in cases where I use the CZ modifier, and in my mind B-B should not be necessary to use since the four surfaces shall be interpreted as one surface already.
But recently one of my colleague attended a GPS training course and the trainer told my colleague to use B-B. So I'm a bit confused, because I cannot find any examples of this in ISO. I have used "B-B" for e.g. hole patterns. So if anyone can point me to where I can find what I'm looking for in the standard, I would appreciate it very much.
I'm working with ISO GPS, but I assume there are some similarity between ISO and ASME in this regard.
a)
b)
In this case, Datum B is a group of four faces. Should I use B or B-B?
I have always used B in cases where I use the CZ modifier, and in my mind B-B should not be necessary to use since the four surfaces shall be interpreted as one surface already.
But recently one of my colleague attended a GPS training course and the trainer told my colleague to use B-B. So I'm a bit confused, because I cannot find any examples of this in ISO. I have used "B-B" for e.g. hole patterns. So if anyone can point me to where I can find what I'm looking for in the standard, I would appreciate it very much.
I'm working with ISO GPS, but I assume there are some similarity between ISO and ASME in this regard.
a)
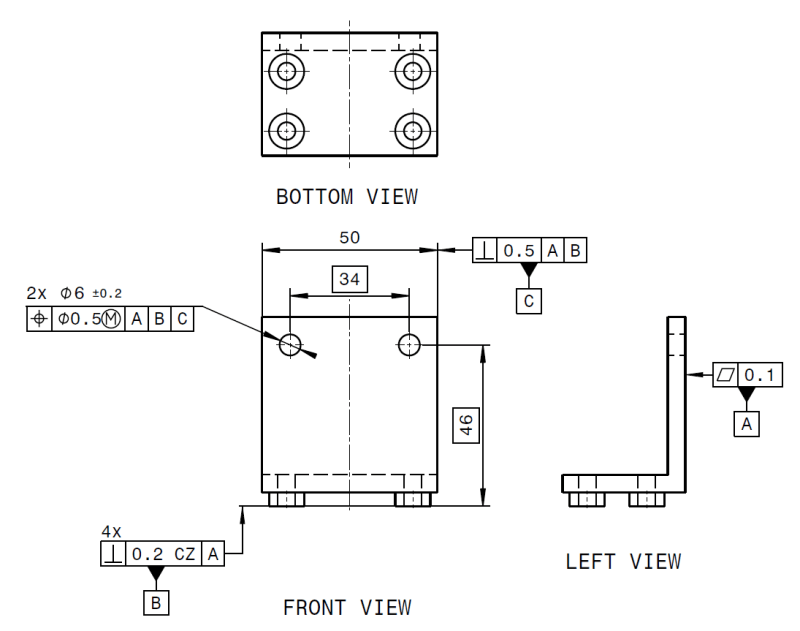
b)
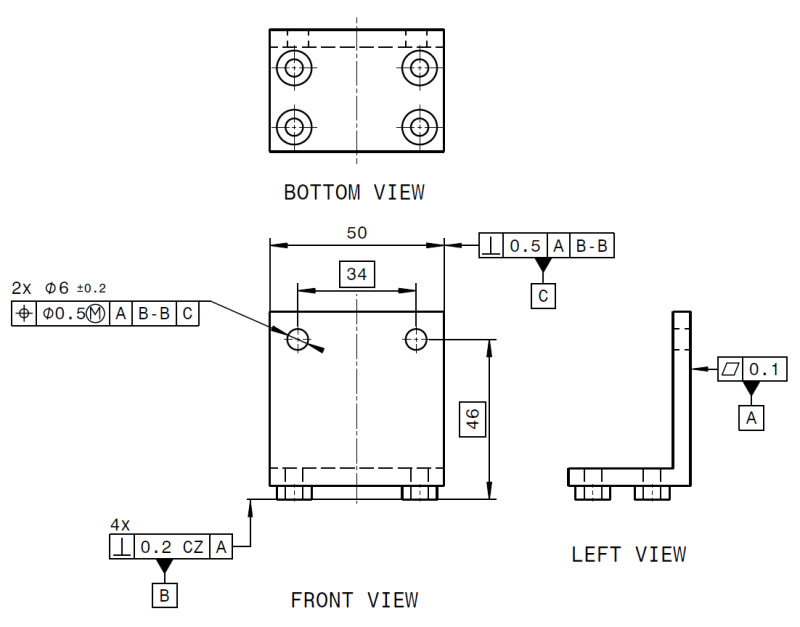