So there is this problem in the PE structural practice exam (NCEES). And I did my calculations and I'm not getting the same result.
The "official" solution is this:
Now here is my approach.
This is a simple AISC 360-10 F11 Rectangular bar yielding check.
The leg that has the load will bend where the moment is maximum and the cross-section of the leg is smallest. This is at a distance k from the bottom corner.
So my calculation was identical to the "official" solution, except that when dividing the moment y the moment arm, I used 3.125 (4- 7/8) in stead of the 3.8125 (4- 3/16).
To me it just doesn't make any reasonable sense that the angle will bend at a thicker cross-section. I've seen the fabrication process for making 60-degree angles, and they always bend at k.
So I'm getting 2.19 for the LRFD result.
There is also this topic, where a user takes a totally wrong approach by assuming the moment is applied at the outer face of the corner.
Am I missing something here?
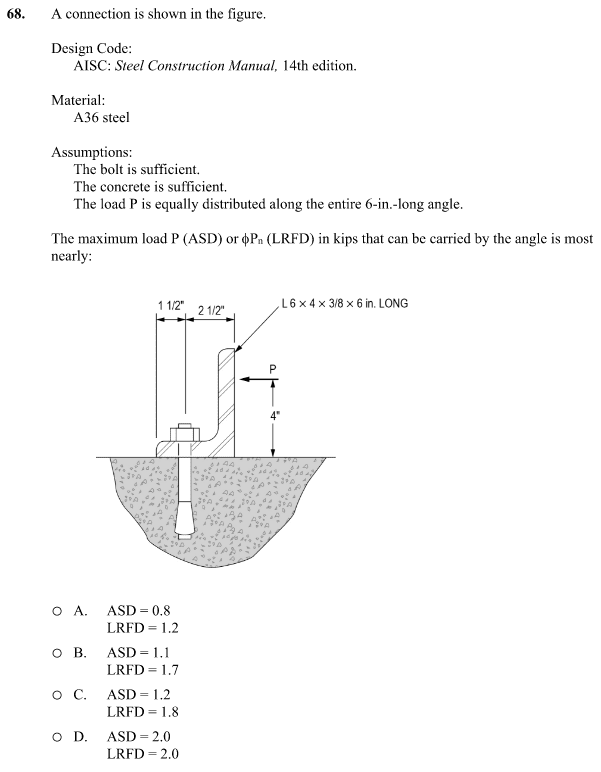
The "official" solution is this:
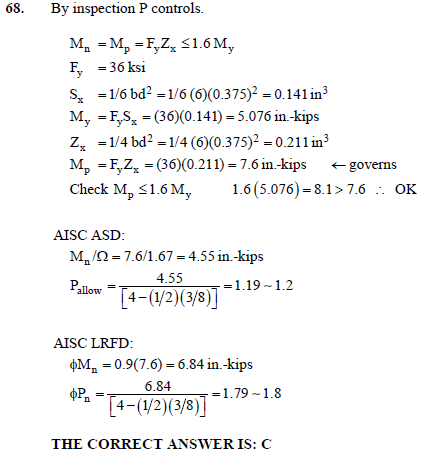
Now here is my approach.
This is a simple AISC 360-10 F11 Rectangular bar yielding check.
The leg that has the load will bend where the moment is maximum and the cross-section of the leg is smallest. This is at a distance k from the bottom corner.
So my calculation was identical to the "official" solution, except that when dividing the moment y the moment arm, I used 3.125 (4- 7/8) in stead of the 3.8125 (4- 3/16).
To me it just doesn't make any reasonable sense that the angle will bend at a thicker cross-section. I've seen the fabrication process for making 60-degree angles, and they always bend at k.
So I'm getting 2.19 for the LRFD result.
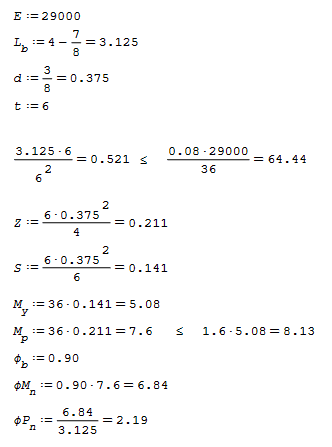
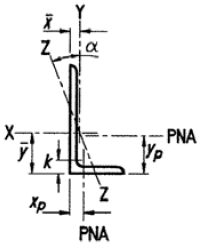

There is also this topic, where a user takes a totally wrong approach by assuming the moment is applied at the outer face of the corner.
Am I missing something here?