JStructsteel
Structural
Truss reactions provided are as shown. What is the RL? I am thinking lateral, but not 100%. W=5"8 is that the bearing width?(2x6 top plate)
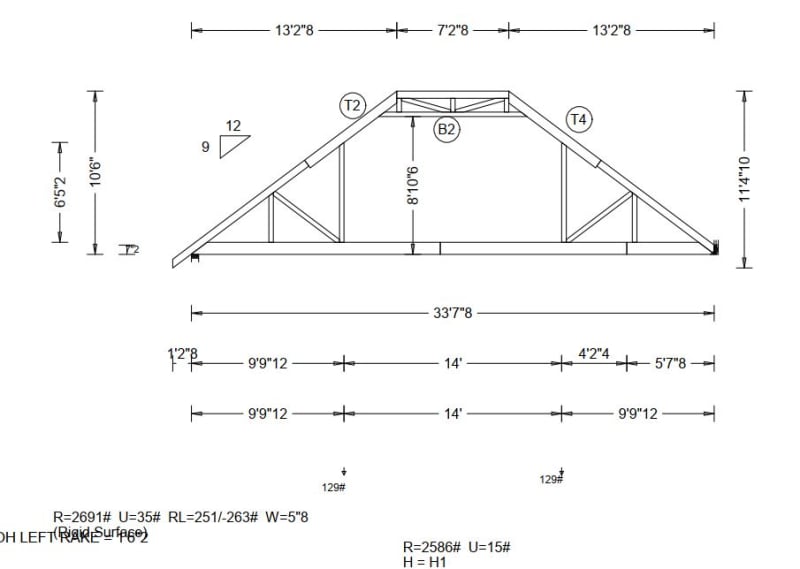
Follow along with the video below to see how to install our site as a web app on your home screen.
Note: This feature may not be available in some browsers.
TheRick109 said:RL probably means "Roof Live Load"
Redneck Ron said:Even at that - If our gravity loads are 50# (30 PSF live and 10 PSF dead) - Wind loads may only be a fraction of that. So if doesn't affect the design of the truss much.
bigmig said:Also, there should be no horizontal reaction. You need to call your truss shop and tell them to design the
truss with one end as a roller.
CrabbyT said:If you have a pin and roller, the pin will pick up the entire horizontal reaction.
XR250 said:Actually, the roof diaphragm picks it up
phamENG said:The 'roller' effect comes not from actually releasing the truss reaction, but from the lack of lateral resistance/stiffness in the wall that is pinned at the foundation and pinned at the truss. The reaction shown on that truss diaphragm is more about the load delivered to the LFRS and not the load delivered to the wall. The wall delivers load to the truss on its way to the diaphragm.