RodRico
Automotive
- Apr 25, 2016
- 508
I just filed a fourth patent addressing fuel injection and charge homogeneity in my engine design, particularly in small versions. Constructive criticism is welcome and is in fact solicited.
This approach injects into a mixing chamber to create a rich charge (stoichiometric in the smallest engine) then injects the charge into the cylinders where it mixes with air to yield the desired equivalence (0.46 max). The mixing chamber averages injector variance, the charge injected into the cylinder is of significant volume which reduces the impact of manufacturing tolerance, and the fact that the injected charge is premixed yields a much better final mix in the combustion chamber. Note the final count of injectors, the configuration of the mixing blades, and the pressure at which the premixed charge is injected into the cylinders are currently undefined and will be determined by CFD.
Note I filed the patent defensively... I don't care if it's patented, I just don't want someone else to patent it and thus prevent me from using it. It used to be that one could simply publish to prevent others from patenting something, but I understand that's not always the case under the America Invents Act. There's a lot of prior art in the approach and that makes me believe it's not patentable, but it does have two-stage injection that I couldn't find in prior art, so I spent the $75 and file a provisional.
This approach injects into a mixing chamber to create a rich charge (stoichiometric in the smallest engine) then injects the charge into the cylinders where it mixes with air to yield the desired equivalence (0.46 max). The mixing chamber averages injector variance, the charge injected into the cylinder is of significant volume which reduces the impact of manufacturing tolerance, and the fact that the injected charge is premixed yields a much better final mix in the combustion chamber. Note the final count of injectors, the configuration of the mixing blades, and the pressure at which the premixed charge is injected into the cylinders are currently undefined and will be determined by CFD.
Note I filed the patent defensively... I don't care if it's patented, I just don't want someone else to patent it and thus prevent me from using it. It used to be that one could simply publish to prevent others from patenting something, but I understand that's not always the case under the America Invents Act. There's a lot of prior art in the approach and that makes me believe it's not patentable, but it does have two-stage injection that I couldn't find in prior art, so I spent the $75 and file a provisional.
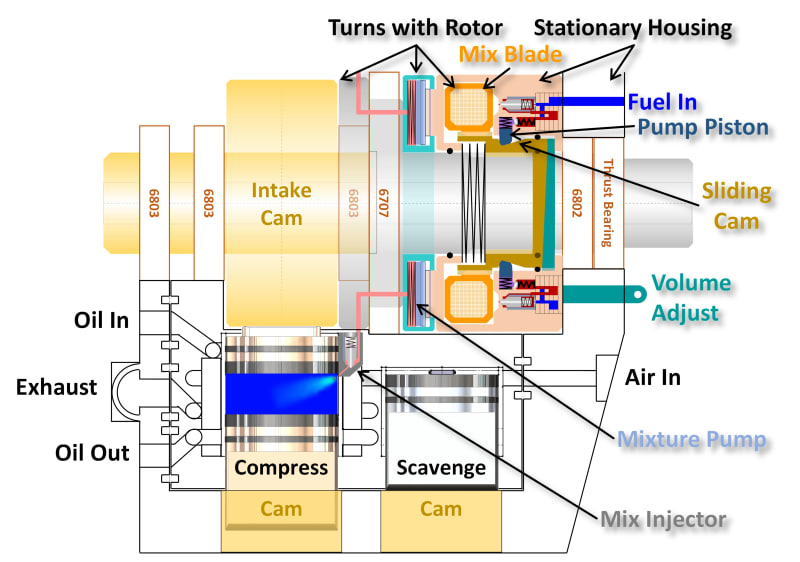