-
1
- #1
Picture elevator to the left and stabilizer to the right.
The red cirkel is a tourque tube on the rudder and have a diameter of 38 mm and the thickness is 1 mm.
The operating horn was a welded box design using steel sheet AISI 4130 in condition N thickness is 1 mm welded against the tourque tube.
On the uperside and sides (3/4 of the circumference) has 30% of the normal materiels strenght(severe lack of fusion).
The last 1/4 can be brittle or have been sheared.
The red triangle is the mechanical stop maximum up.
The relationship between hinge, tourquetube and elevetor edge ca..
0 --------1 --------------------7
Can this construction hold for 5,7 G ???
[img [URL unfurl="true"]https://res.cloudinary.com/engineering-com/image/upload/v1604784211/tips/STABH2_lpxbcz.jpg[/URL]
Properties Metric Imperial
Tensile strength, ultimate 560 MPa 81200 psi
Tensile strength, yield 460 MPa 66700 psi
Modulus of elasticity 190-210 GPa 27557-30458 ksi
Bulk modulus (Typical for steel) 140 GPa 20300 ksi
Shear modulus (Typical for steel) 80 GPa 11600 ksi
Poissons ratio 0.27-0.30 0.27-0.30
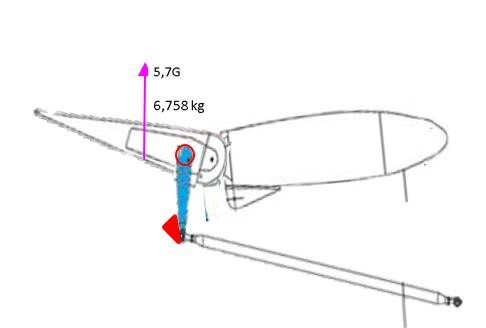
The red cirkel is a tourque tube on the rudder and have a diameter of 38 mm and the thickness is 1 mm.
The operating horn was a welded box design using steel sheet AISI 4130 in condition N thickness is 1 mm welded against the tourque tube.
On the uperside and sides (3/4 of the circumference) has 30% of the normal materiels strenght(severe lack of fusion).
The last 1/4 can be brittle or have been sheared.
The red triangle is the mechanical stop maximum up.
The relationship between hinge, tourquetube and elevetor edge ca..
0 --------1 --------------------7
Can this construction hold for 5,7 G ???
[img [URL unfurl="true"]https://res.cloudinary.com/engineering-com/image/upload/v1604784211/tips/STABH2_lpxbcz.jpg[/URL]
Properties Metric Imperial
Tensile strength, ultimate 560 MPa 81200 psi
Tensile strength, yield 460 MPa 66700 psi
Modulus of elasticity 190-210 GPa 27557-30458 ksi
Bulk modulus (Typical for steel) 140 GPa 20300 ksi
Shear modulus (Typical for steel) 80 GPa 11600 ksi
Poissons ratio 0.27-0.30 0.27-0.30