-
1
- #1
Burunduk
Mechanical
- May 2, 2019
- 2,483
The two most recent versions ('09 and '18) of ASME Y14.5 define a 'datum' as:
In past discussions such as thread1103-452649 no clear conclusion was reached about what can be the intent behind the addition of "line" to the definition in the '09 edition of the standard.
Please see the following diagram.
Do you think, based on the Y14.5 standard, that the shown curved line could be a valid datum corresponding specifically to the "line" type (and only) in the above definition? If not, why?
With "line" mentioned as a separate kind.Y14.5 said:datum: a theoretically exact point, axis, line, plane, or combination thereof derived from the true geometric counterpart.
In past discussions such as thread1103-452649 no clear conclusion was reached about what can be the intent behind the addition of "line" to the definition in the '09 edition of the standard.
Please see the following diagram.
Do you think, based on the Y14.5 standard, that the shown curved line could be a valid datum corresponding specifically to the "line" type (and only) in the above definition? If not, why?
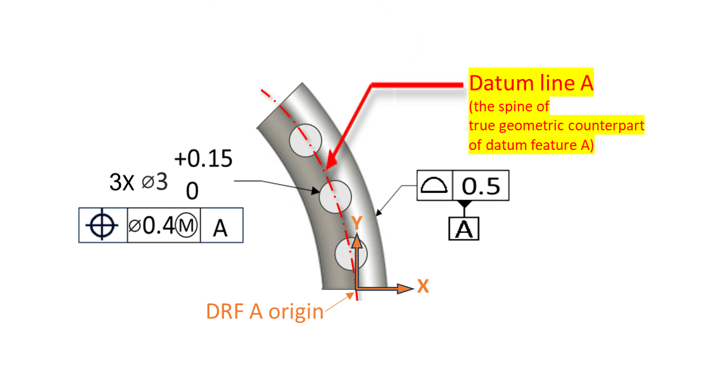