emerald11
Mechanical
- Nov 26, 2017
- 8
Hi!
I have constructed a simple hydralic system (on paper) that should be able to open a cargo door.
As you can see it will have 2 lifting cylinders. To open the cargo door a force of 45kN is required for each cylinder.
The stroke has to me 600mm.
The pump that will be used:
Deplacement : 24cm3 /revolution
max pressure : 200bar
efficiencies for the pump is nvol 95%, nhm 95%.
initial speed of the pump is 1100 rpm
I have an hard time finding good cylinders that are fairly common on the market for this job.
What cylinders would be best for this job? Model name? (so i can order it and download the data sheet).
Thanks in advance.
I have constructed a simple hydralic system (on paper) that should be able to open a cargo door.
As you can see it will have 2 lifting cylinders. To open the cargo door a force of 45kN is required for each cylinder.
The stroke has to me 600mm.
The pump that will be used:
Deplacement : 24cm3 /revolution
max pressure : 200bar
efficiencies for the pump is nvol 95%, nhm 95%.
initial speed of the pump is 1100 rpm
I have an hard time finding good cylinders that are fairly common on the market for this job.
What cylinders would be best for this job? Model name? (so i can order it and download the data sheet).
Thanks in advance.
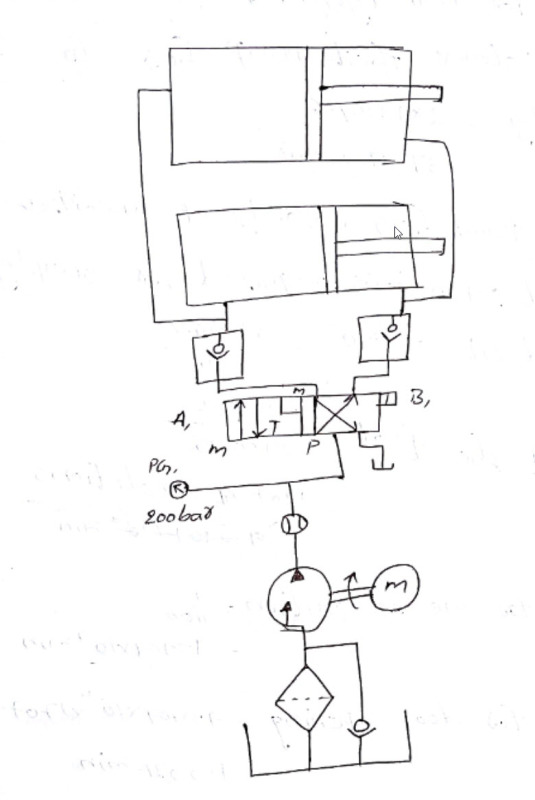