StrEng007
Structural
- Aug 22, 2014
- 543
I have a building that features s pop up roof section. Please see the image below.
Long story short, I have a hole right in the middle of my roof diaphragm. Based on the shear wall layout, there is no vertical element to support the edges of the roof diaphragm shown as #1 and #2.
Would this be a candidate for each diaphragm to be treated as an "open front diaphragm"?
In all the design examples I've seen, the open front end of the diaphragm didn't have an additional "point load" in the transverse direction.
Additionally, what I'm not showing is the fact this roof is a gable. I've shown it as being flat because that helps me first get an understanding of the approach I want to take. My second concern here is being able to get a 3 sided diaphragm to work as a gable roof with a steep slope.
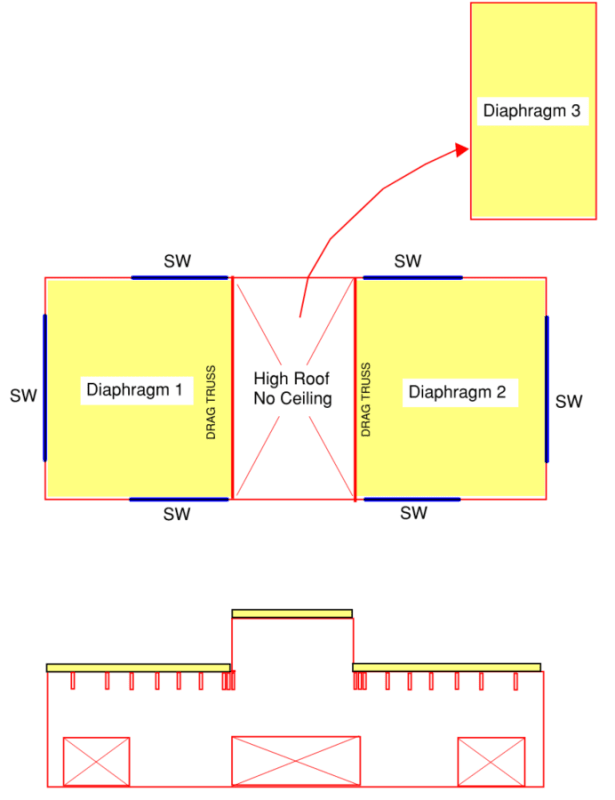
Long story short, I have a hole right in the middle of my roof diaphragm. Based on the shear wall layout, there is no vertical element to support the edges of the roof diaphragm shown as #1 and #2.
Would this be a candidate for each diaphragm to be treated as an "open front diaphragm"?
In all the design examples I've seen, the open front end of the diaphragm didn't have an additional "point load" in the transverse direction.
Additionally, what I'm not showing is the fact this roof is a gable. I've shown it as being flat because that helps me first get an understanding of the approach I want to take. My second concern here is being able to get a 3 sided diaphragm to work as a gable roof with a steep slope.