akkamaan
Agricultural
- Jun 20, 2010
- 111
For a hydraulic guy to say that pressure is created by resistance to flow is like an electrician would say that the resistor creates the voltage...Right!?![[ponder] [ponder] [ponder]](/data/assets/smilies/ponder.gif)
![[bigglasses] [bigglasses] [bigglasses]](/data/assets/smilies/bigglasses.gif)
Listen to
Jim Pytel, Columbia Gorge Community College
in his Youtube lesson
LunchBoxSession
Insane Hydraulics
![[ponder] [ponder] [ponder]](/data/assets/smilies/ponder.gif)
![[bigglasses] [bigglasses] [bigglasses]](/data/assets/smilies/bigglasses.gif)
Listen to
Jim Pytel, Columbia Gorge Community College
in his Youtube lesson
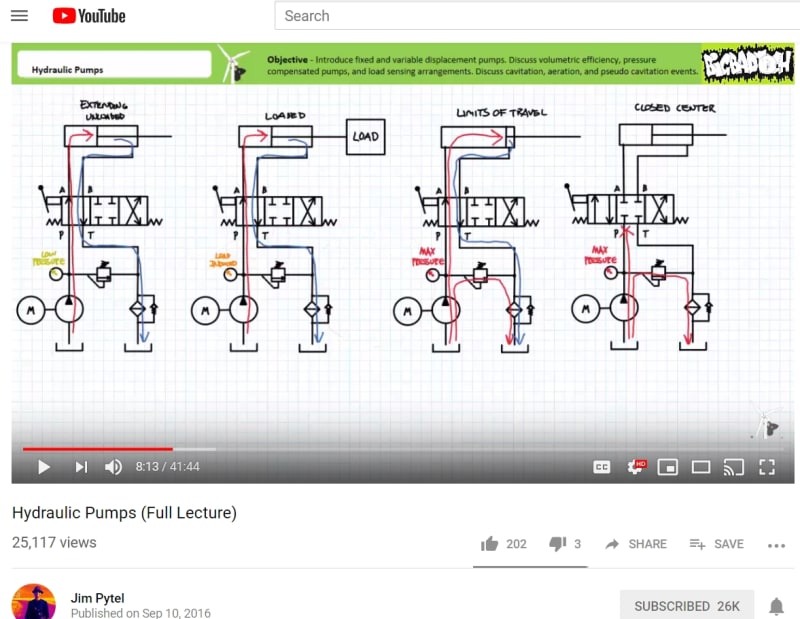
LunchBoxSession
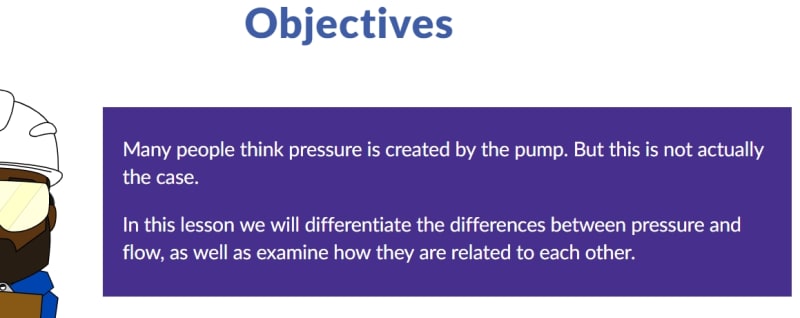
Insane Hydraulics
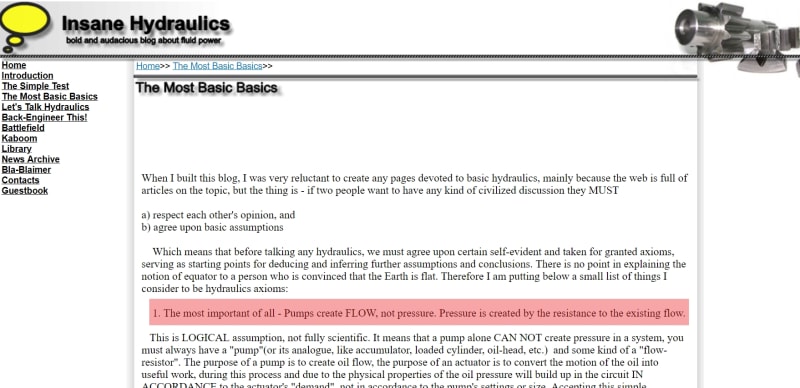