Harry Houdini
Aerospace
Good afternoon fellow engineers. I had a quick question regarding the contents of this drawings GENERAL NOTES. I want to know if anything that I defined in the general drawing notes directly violates anything withing ASME Y14 Standards.
[ul]
[li]Every part will be sent to a manufacturer with a STEP file and a PDF of the technical drawing.[/li]
[li]We are using an ALL OVER profile tolerance with datums.[/li]
[li]Every drawing will have datums on it.[/li]
[li]Drawing may or may not be completely fully defined by dimensions on the sheet[/li]
[li]When dimensions are not shown, any missing dimension or value should be grabbed from the CAD Model[/li]
[li]If a value is pulled from the model, then it should be considered BASIC because I want the value to have a tolerance based off of the profile[/li]
[li]We currently have an issue where a decent amount of drawings are note fully defined by drawing dimensions (which manufacturers are okay with) but we have a machinist who does everything by hand, so he requires fully dimensioned drawings. This led to the reference dimension section about how they are BASIC. I am super uneasy about this and I think it may clash with ASME.[/li]
[/ul]
[ul]
[li]Every part will be sent to a manufacturer with a STEP file and a PDF of the technical drawing.[/li]
[li]We are using an ALL OVER profile tolerance with datums.[/li]
[li]Every drawing will have datums on it.[/li]
[li]Drawing may or may not be completely fully defined by dimensions on the sheet[/li]
[li]When dimensions are not shown, any missing dimension or value should be grabbed from the CAD Model[/li]
[li]If a value is pulled from the model, then it should be considered BASIC because I want the value to have a tolerance based off of the profile[/li]
[li]We currently have an issue where a decent amount of drawings are note fully defined by drawing dimensions (which manufacturers are okay with) but we have a machinist who does everything by hand, so he requires fully dimensioned drawings. This led to the reference dimension section about how they are BASIC. I am super uneasy about this and I think it may clash with ASME.[/li]
[/ul]
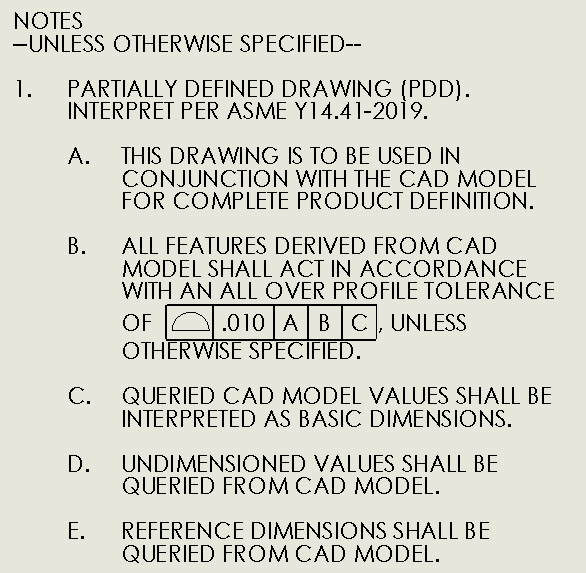