OK ... here is a dumb one.
I need a temporary slide.
I need to get 96 pieces of metal roofing ... 16" wide x 38 ft long ... to a roof. The edge of the roof is about 18 ft off the round.
The metal is super flexible ... if it bends, it is garbage ... If you hold one end straight up, the other will fall over.
It is not heavy ... about 40 lbs per piece.
So, I am thinking of a cart ... 40 ft long ... can slide them out of the crate and onto it. Then I can use it like a wheelbarrow ... move it over (about 50 ft) to the building ... then lift one end (I have a man lift on site) ... finally sliding up and onto the roof.
OK ... sound like work but I have put every nail into this shop so far .. even got the trusses up myself ....
Anyway, my question ...
If I make a cart out of say PVC pipe ...the side (about 2 ft high) would need to be like a floor truss to make it stiff.
Without going through hours of calculations ... is there a best arrangement for the memembers.
Attached is an image shown a couple of layouts .... there are many many ways to go ... is one "stronger" (less flexible) than another?
Just looking for some practical advice.
You can see videos of my build on my facebook page: Link
Thanks ....
I need a temporary slide.
I need to get 96 pieces of metal roofing ... 16" wide x 38 ft long ... to a roof. The edge of the roof is about 18 ft off the round.
The metal is super flexible ... if it bends, it is garbage ... If you hold one end straight up, the other will fall over.
It is not heavy ... about 40 lbs per piece.
So, I am thinking of a cart ... 40 ft long ... can slide them out of the crate and onto it. Then I can use it like a wheelbarrow ... move it over (about 50 ft) to the building ... then lift one end (I have a man lift on site) ... finally sliding up and onto the roof.
OK ... sound like work but I have put every nail into this shop so far .. even got the trusses up myself ....
Anyway, my question ...
If I make a cart out of say PVC pipe ...the side (about 2 ft high) would need to be like a floor truss to make it stiff.
Without going through hours of calculations ... is there a best arrangement for the memembers.
Attached is an image shown a couple of layouts .... there are many many ways to go ... is one "stronger" (less flexible) than another?
Just looking for some practical advice.
You can see videos of my build on my facebook page: Link
Thanks ....
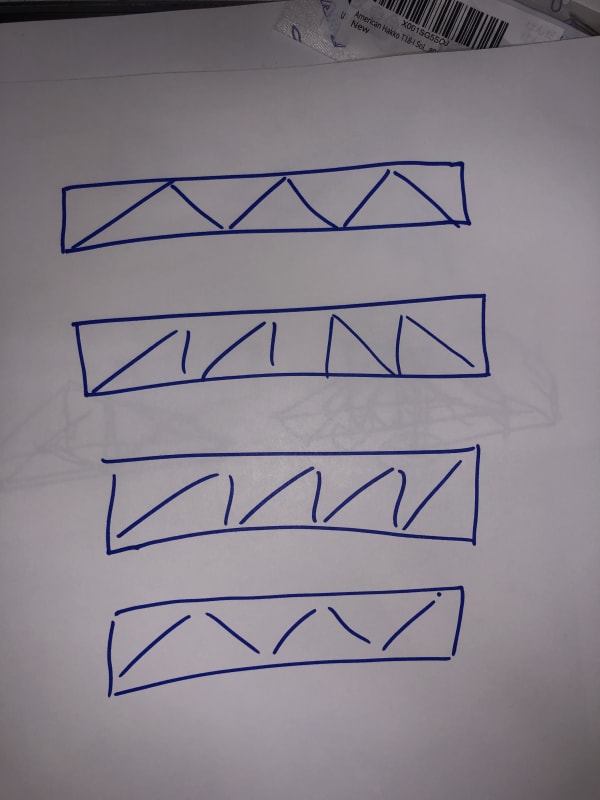