edison123
Electrical
- Oct 23, 2002
- 4,506
For a crane long travel along a factory length, in terms of load carrying and resisting torsion while the crane moves, is a I beam of hxw with one vertical web of thickness t is better than a box beam of same hxw with two vertical webs of thickness t each as shown below? Crane supplier claims I beam is better. Both are fabricated from structural steel.
Muthu
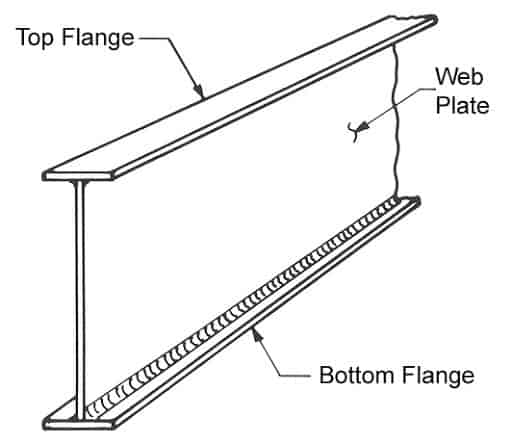
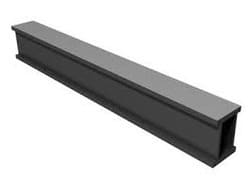
Muthu