I'm looking for some ideas from the Brain Trust.
I'm building a high energy off-grid power source. It has lithium batteries. Of course the finicky lithiums cannot be over charged or over-discharged or charged when too cold (on pain of death to lots of things including one's wallet) The system's Battery Management System (BMS) needs the ability to cut the power to and from the batteries. Commonly used for this are the typical power solenoid relays:
But those are abhorrent because they consume a ton of energy just being kept closed. They typically are too hot to touch making them scandalously power wasting. Not doing that.
Much much better is a motorized disconnect that ceases to draw any power after it's open or closed.
I use these cool valves frequently. Look at the price for a stainless steel ball valve version!!
Amazing! So now turning to switching electricity instead of water, a much more trivial effort made of some stamped metal contacts and a little bending of it and you get this:
The problem is that ridiculous price! I'm not doing that. I need about 10 of these. But damned if I'm paying that exorbitant price for it.
Here's the non-motorized price.
While OFF and ON would be nice I can live with OFF only. This means a solenoid type action where a PLC generates a brief ON could maybe pull something. Perhaps something like one of these kill switches.
Or perhaps twist something like one of these:
Or pulls open one of these:
I could run a motor too.
I have a couple of 3D printers and I'm not afraid to use them
I can print most any cam, lever, shaft, housing, frame, linkage, or mechanism.
Suggestions?
Keith Cress
kcress -
I'm building a high energy off-grid power source. It has lithium batteries. Of course the finicky lithiums cannot be over charged or over-discharged or charged when too cold (on pain of death to lots of things including one's wallet) The system's Battery Management System (BMS) needs the ability to cut the power to and from the batteries. Commonly used for this are the typical power solenoid relays:
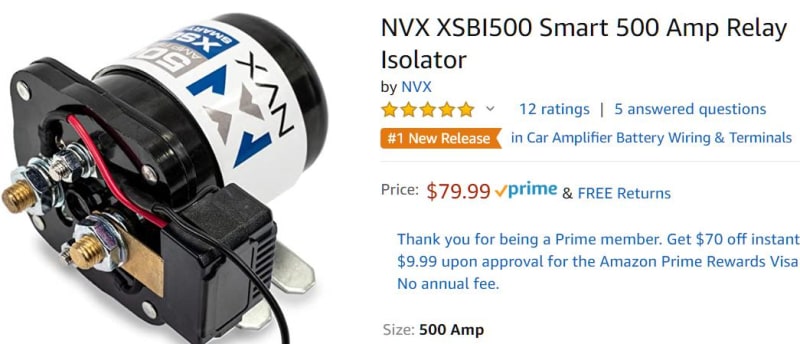
But those are abhorrent because they consume a ton of energy just being kept closed. They typically are too hot to touch making them scandalously power wasting. Not doing that.
Much much better is a motorized disconnect that ceases to draw any power after it's open or closed.
I use these cool valves frequently. Look at the price for a stainless steel ball valve version!!
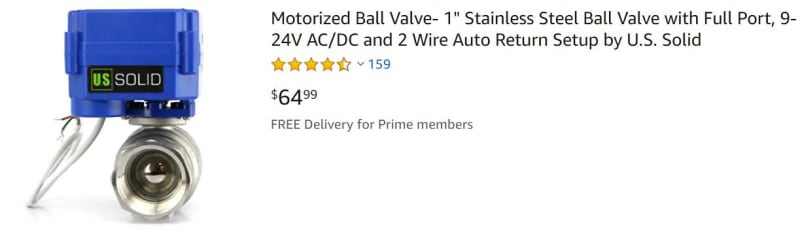
Amazing! So now turning to switching electricity instead of water, a much more trivial effort made of some stamped metal contacts and a little bending of it and you get this:
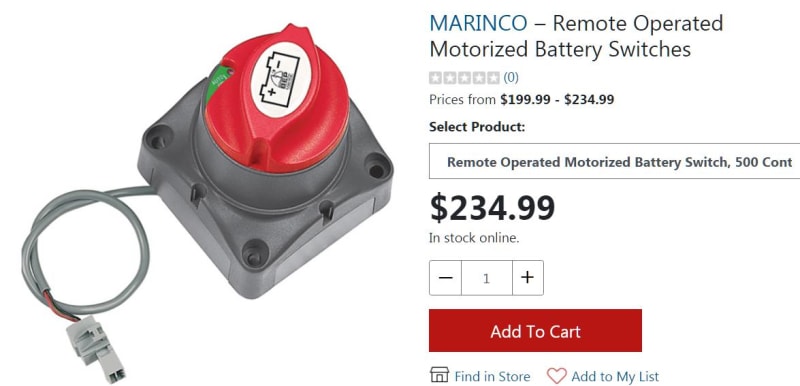
The problem is that ridiculous price! I'm not doing that. I need about 10 of these. But damned if I'm paying that exorbitant price for it.
Here's the non-motorized price.
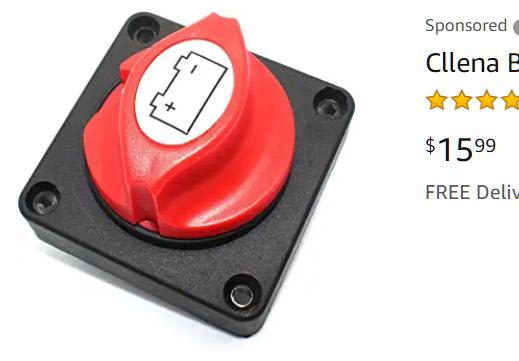
While OFF and ON would be nice I can live with OFF only. This means a solenoid type action where a PLC generates a brief ON could maybe pull something. Perhaps something like one of these kill switches.
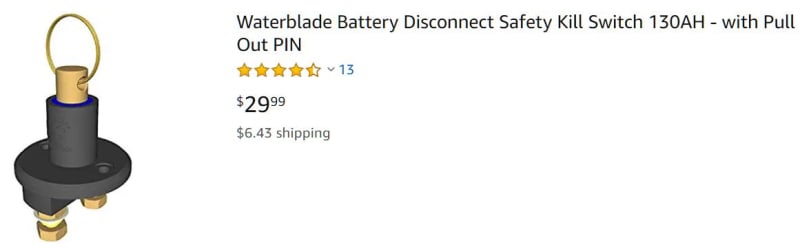
Or perhaps twist something like one of these:
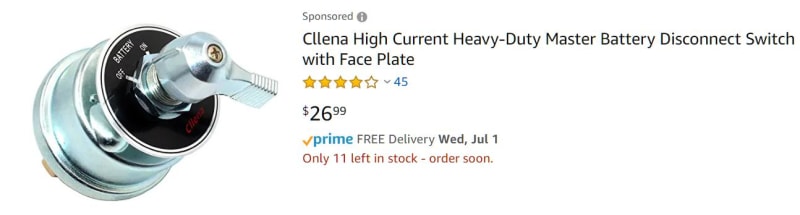
Or pulls open one of these:
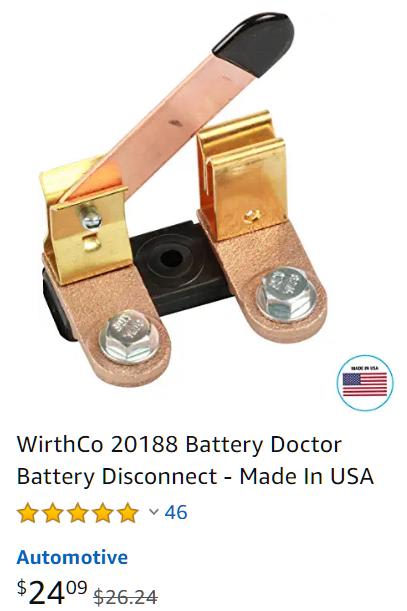
I could run a motor too.
I have a couple of 3D printers and I'm not afraid to use them

Suggestions?
Keith Cress
kcress -