cal91
Structural
- Apr 18, 2016
- 294
I have a case where there is a balcony which is supported from cantilevered steel floor beams. The floor beams tos are flush with their supporting girder steel beams. To provide continuity for the floor beams the flanges are CJP welded to the steel girder.
The top flange of the girder is in compression at the intersection with the floor beam (mid simple span). The top flange of the cantilevering floor beam is in tension.
I'm assuming I cannot have both the girder and floor beam both be at full capacity at the same location, and I can use Mohr's circle to understand what stresses are in the beam, but I'm not sure if there are any interaction provisions our design methods prescribed by AISC.
Any thoughts? Thanks in advance.
Edit: Here's the plan view.
The top flange of the girder is in compression at the intersection with the floor beam (mid simple span). The top flange of the cantilevering floor beam is in tension.
I'm assuming I cannot have both the girder and floor beam both be at full capacity at the same location, and I can use Mohr's circle to understand what stresses are in the beam, but I'm not sure if there are any interaction provisions our design methods prescribed by AISC.
Any thoughts? Thanks in advance.
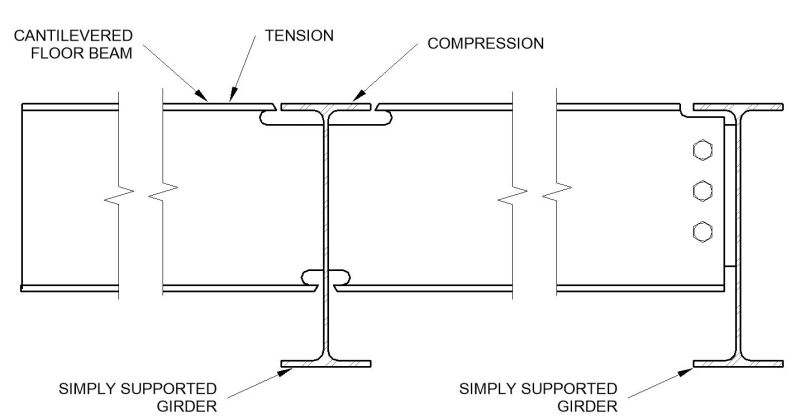
Edit: Here's the plan view.
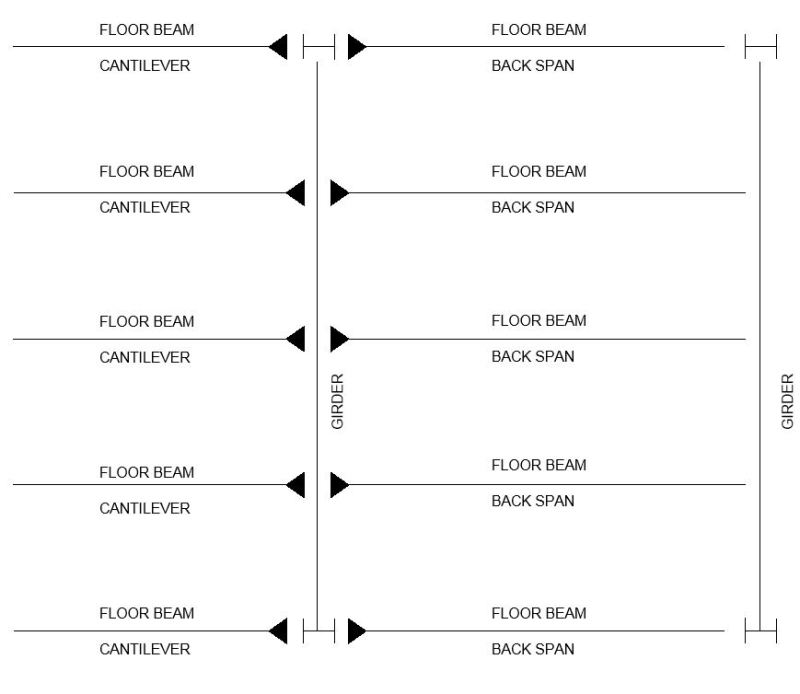