I re-created this drawing for illustration purposes. All the flat sides/surfaces are actually not flat (so cannot be used as datums).
The intention is for dia4 hole to be perpendicular to curved surface (R10). But is this FCF correct? (whether by ASME or ISO)
If Datum A was re-defined as a specific line on this curved surface, would it be legal? (But it would be difficult to measure also)
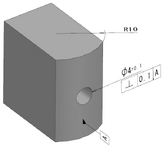
The intention is for dia4 hole to be perpendicular to curved surface (R10). But is this FCF correct? (whether by ASME or ISO)
If Datum A was re-defined as a specific line on this curved surface, would it be legal? (But it would be difficult to measure also)
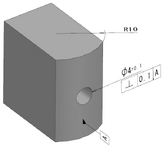