Burunduk
Mechanical
- May 2, 2019
- 2,513
Fig. 4-31, ASME Y14.5, illustration (c):
"Datum feature B must remain in contact at a minimum one point."
With this condition, It looks like if the profile tolerance applied on datum feature B was more than the shown 0.2 and large enough, or the position tolerance for the holes was less than 0.3(M) and tight enough, a pair of holes positioned accurately and passing inspection per the (a) and (b) cases, may be forced out of tolerance by rotating the part all the way to meet the requirement of minimum one point of contact with the datum feature simulator of B at MMB. Perhaps this can be prevented by having the datum feature B toleranced considerably more accurately than the holes controlled with reference to it, but it still seems weird; It looks like MMB and the minimum contact requirement in this case actually make it more difficult to meet the tolerance - unlike for example the case of 4-30 (b) where the scheme makes sense because there is actual datum shift. MMB in fig. 4-31 seems to impose a restriction rather than allowing shift. Where am I wrong?
"Datum feature B must remain in contact at a minimum one point."
With this condition, It looks like if the profile tolerance applied on datum feature B was more than the shown 0.2 and large enough, or the position tolerance for the holes was less than 0.3(M) and tight enough, a pair of holes positioned accurately and passing inspection per the (a) and (b) cases, may be forced out of tolerance by rotating the part all the way to meet the requirement of minimum one point of contact with the datum feature simulator of B at MMB. Perhaps this can be prevented by having the datum feature B toleranced considerably more accurately than the holes controlled with reference to it, but it still seems weird; It looks like MMB and the minimum contact requirement in this case actually make it more difficult to meet the tolerance - unlike for example the case of 4-30 (b) where the scheme makes sense because there is actual datum shift. MMB in fig. 4-31 seems to impose a restriction rather than allowing shift. Where am I wrong?
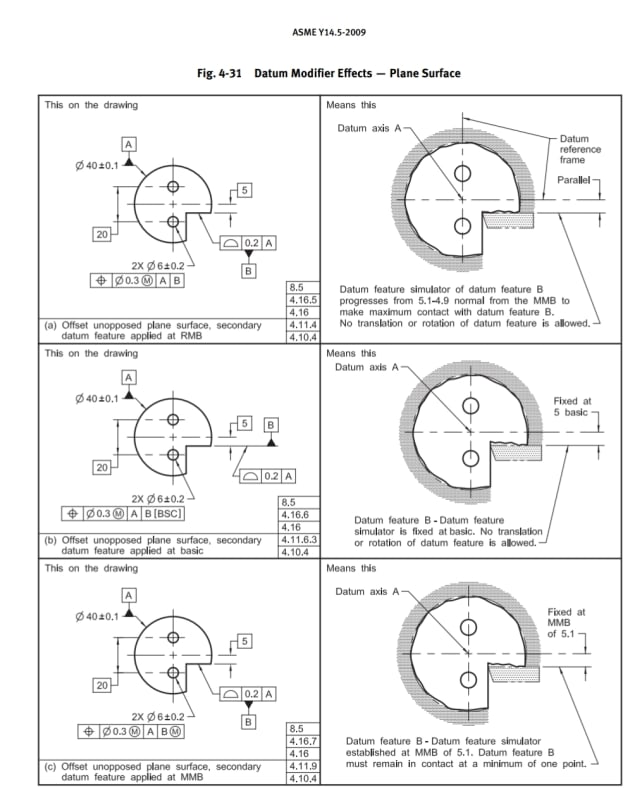