unclebensrice
Petroleum
Dear all,
Whenever Pump B comes online, pressure on Pump A goes up and trips it. is there anything that can be done to resolve this? both pumps need to be working simultaneously.
thanks.
Whenever Pump B comes online, pressure on Pump A goes up and trips it. is there anything that can be done to resolve this? both pumps need to be working simultaneously.
thanks.
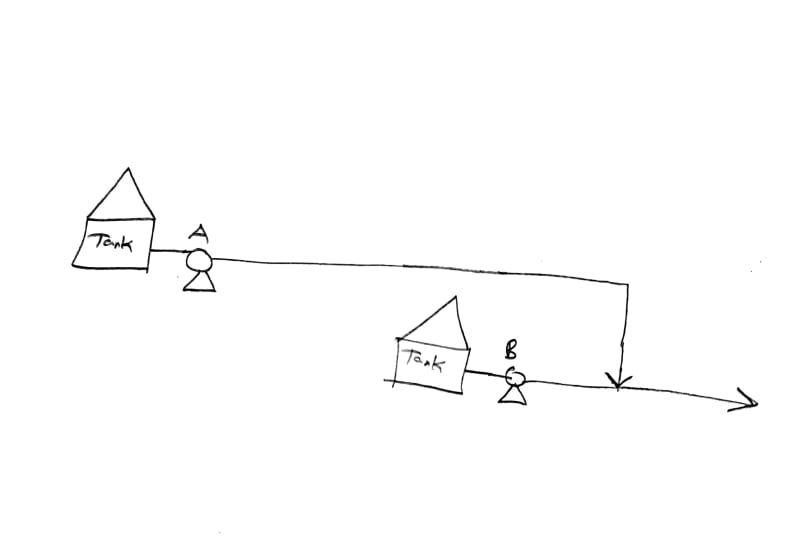