Hi all
I am modelling a composite tube under tensile deformation. My material coordinates, and element coordinates are right. I have applied a tensile load of 5kN at one end of the specimen while fixing the other end.
I am not sure how to extrapolate the reaction forces. I am using the constraint forces that generate at the fixed end to determine the axial modulus, and using the maximum tensile displacement in x direction for calculating strains.
My axial modulus is coming out to be 5 times higher than it should be. I have a configuration of [0,45,-45] and which is impossible. I am using cylindrical coordinate system and have aligned everything along R direction
Can anyone advice ? I am attaching some images.
I am modelling a composite tube under tensile deformation. My material coordinates, and element coordinates are right. I have applied a tensile load of 5kN at one end of the specimen while fixing the other end.
I am not sure how to extrapolate the reaction forces. I am using the constraint forces that generate at the fixed end to determine the axial modulus, and using the maximum tensile displacement in x direction for calculating strains.
My axial modulus is coming out to be 5 times higher than it should be. I have a configuration of [0,45,-45] and which is impossible. I am using cylindrical coordinate system and have aligned everything along R direction
Can anyone advice ? I am attaching some images.
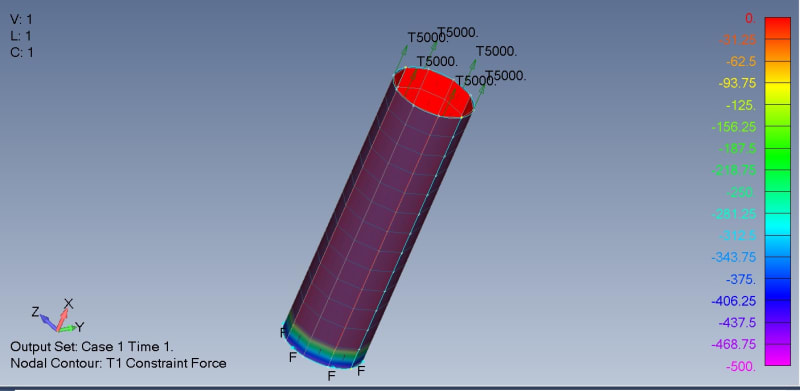
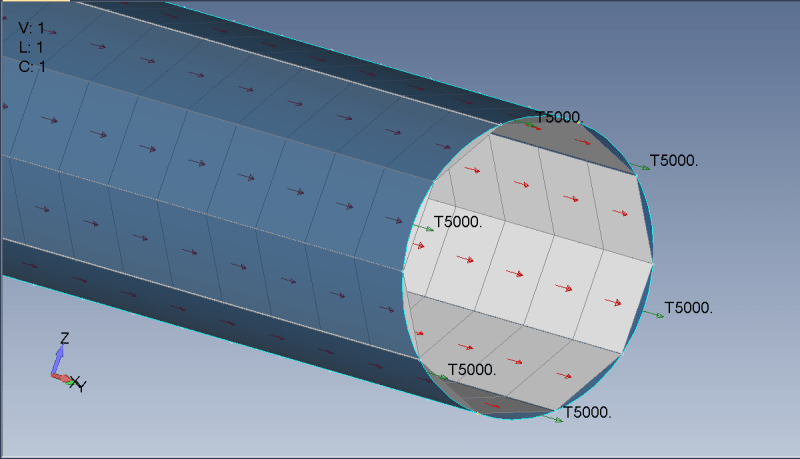
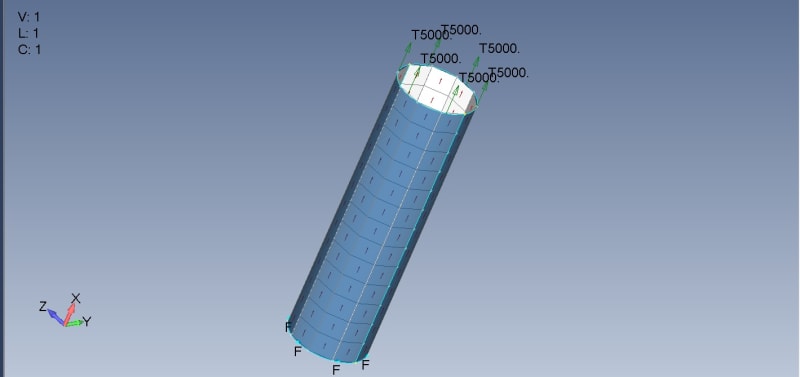
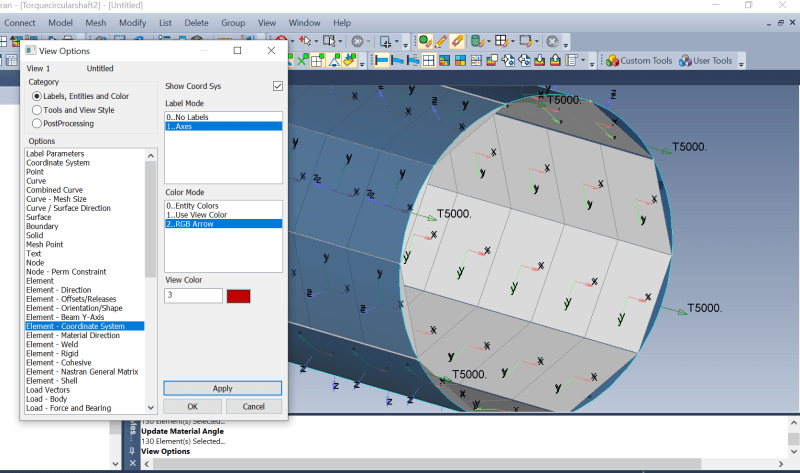