Applying a surface tolerance on a surface without datum reference. Is this flatness? My knowledge is limited in GD&T.
Is this true ? I am having a hard time seeing it.
I want to ensure that the profile of the surface is 1mm. I did not want to reference datums, as I read datums were not required for profile tolerances.
Is this true ? I am having a hard time seeing it.
I want to ensure that the profile of the surface is 1mm. I did not want to reference datums, as I read datums were not required for profile tolerances.
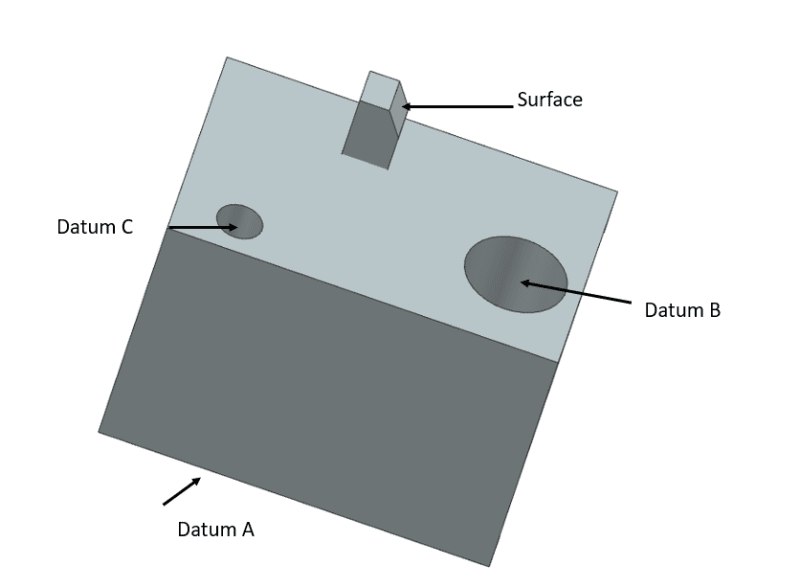