R1chJC
Marine/Ocean
- Apr 15, 2015
- 51
Hi All,
I have a part that looks like a figure of 8 with two holes, similar to a chain link.
The holes need aligning with one another but i'm struggling to decide how to apply a tertiary datum to lock any rotation - see attached.
I don't want the holes wandering off so the wall thickness get reduced.
See attached picture.
Any help would be great.
I have a part that looks like a figure of 8 with two holes, similar to a chain link.
The holes need aligning with one another but i'm struggling to decide how to apply a tertiary datum to lock any rotation - see attached.
I don't want the holes wandering off so the wall thickness get reduced.
See attached picture.
Any help would be great.
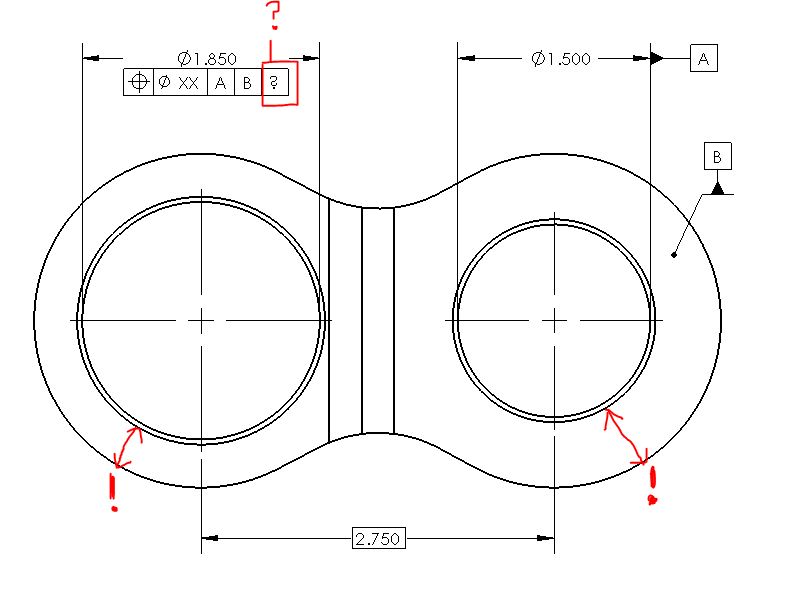