KootK
Structural
- Oct 16, 2001
- 18,561
My situation shown below. This is making me pretty unpopular with the helical pile supplier and the only "outs" that I can think of are to:
1) Use the 2" mud slab like a regular SOG to resist lateral loads.
2) Use the backfill around the base of the wall to resist lateral loads.
Thus far, I've not been willing to do either of these things owing to concerns over of quality and permanence. How do others feel about this? Am I being too much of a hard ass?
1) Use the 2" mud slab like a regular SOG to resist lateral loads.
2) Use the backfill around the base of the wall to resist lateral loads.
Thus far, I've not been willing to do either of these things owing to concerns over of quality and permanence. How do others feel about this? Am I being too much of a hard ass?
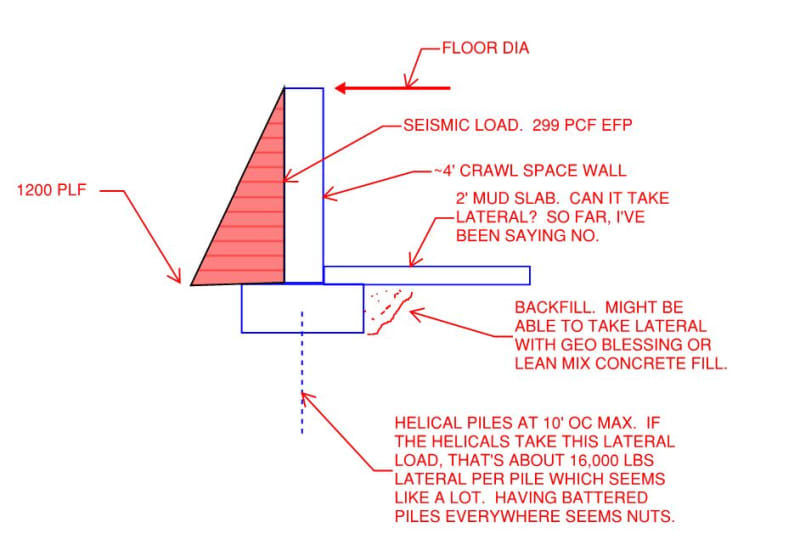