-
1
- #1
semiond
Mechanical
- Jan 9, 2011
- 176
Hello all,
Fig. 4-49 in ASME Y-14.5-2009 displays the use of datum target spheres.
I wanted to know if it is also acceptable to use datum target cylinders. I haven't seen an example in the standard and i'm not sure whether it is allowed or not.
One case where this could be useful is parts with dovetail geometry (see picture); both for controling the dovetail taper surfaces themselves (profile of a surface referencing datum target cylinders with basic dimension distances) and for constraining degrees of freedom and establishing the DRF for the entire part.
Fig. 4-49 in ASME Y-14.5-2009 displays the use of datum target spheres.
I wanted to know if it is also acceptable to use datum target cylinders. I haven't seen an example in the standard and i'm not sure whether it is allowed or not.
One case where this could be useful is parts with dovetail geometry (see picture); both for controling the dovetail taper surfaces themselves (profile of a surface referencing datum target cylinders with basic dimension distances) and for constraining degrees of freedom and establishing the DRF for the entire part.
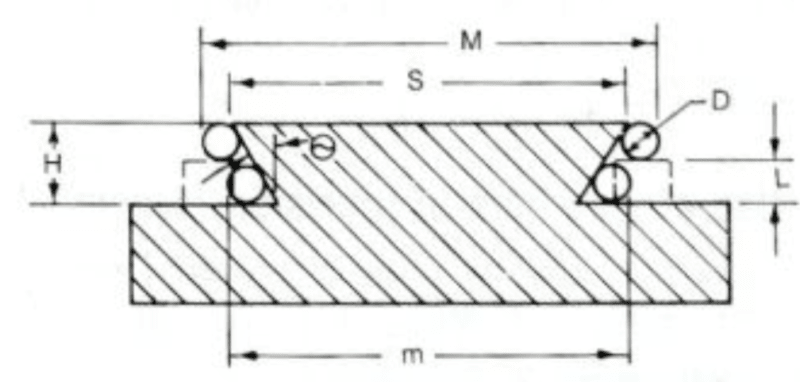