Suppose we have a slab with an offset that at the same time acts as a supporting beam (happens a lot in projects where there is an underground garage for example). In the static analysis the slab is assumed to be continuous. The beam acts as a support therefore the moments in the slab will be negative requiring top reinforcement.
The question: Is it enough to anchor the top reinforcement inside the width of the beam? Or is it necessary to overlap the required reinforcement with the beam stirrups in order to provide continuity of the moment resistance between the top and bottom slabs?
By my estimate, this has to do with the width of the beam (b in the sketch). In sufficiently wide beams (how would that be defined though?) the beam can be assumed as fully rigid and therefore I would expect a mere anchorage of the slab reinforcement to suffice. If the beam is not wide enough (perhaps close to the depth of the slabs) then I would expect a need for overlapping the required reinforcement of the slabs with the beam stirrups so the moment can be fully transferred.
Below I have two sketches: One is the described situation - slab offset as a supporting beam and the second is a typical slab offset with the proposed reinforcement for moment continuity.
The question: Is it enough to anchor the top reinforcement inside the width of the beam? Or is it necessary to overlap the required reinforcement with the beam stirrups in order to provide continuity of the moment resistance between the top and bottom slabs?
By my estimate, this has to do with the width of the beam (b in the sketch). In sufficiently wide beams (how would that be defined though?) the beam can be assumed as fully rigid and therefore I would expect a mere anchorage of the slab reinforcement to suffice. If the beam is not wide enough (perhaps close to the depth of the slabs) then I would expect a need for overlapping the required reinforcement of the slabs with the beam stirrups so the moment can be fully transferred.
Below I have two sketches: One is the described situation - slab offset as a supporting beam and the second is a typical slab offset with the proposed reinforcement for moment continuity.
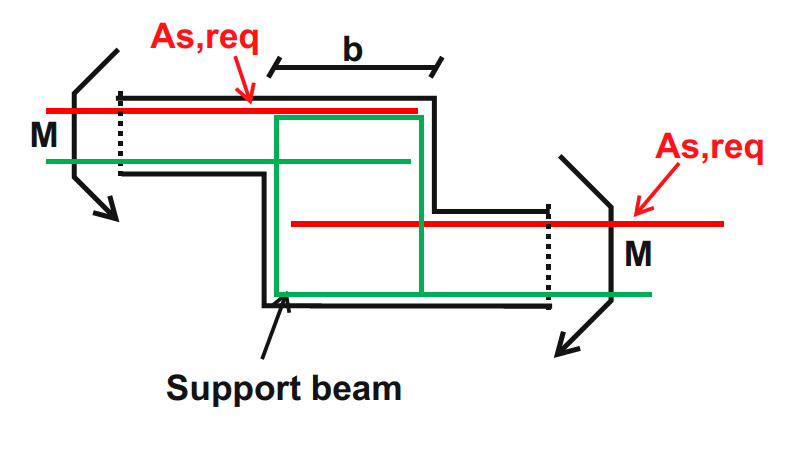
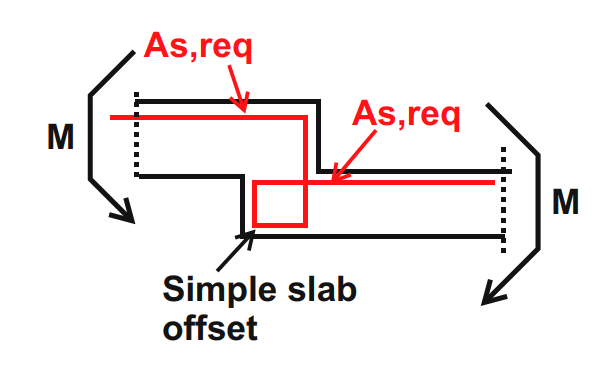