-
1
- #1
Some pretty serious looking issues here.
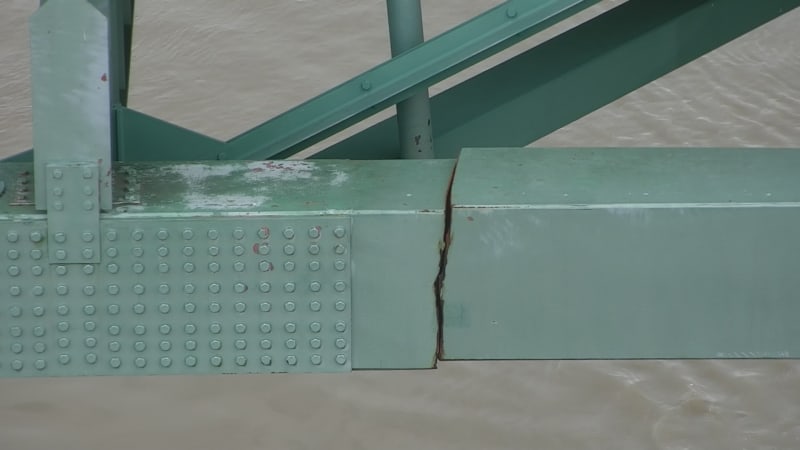
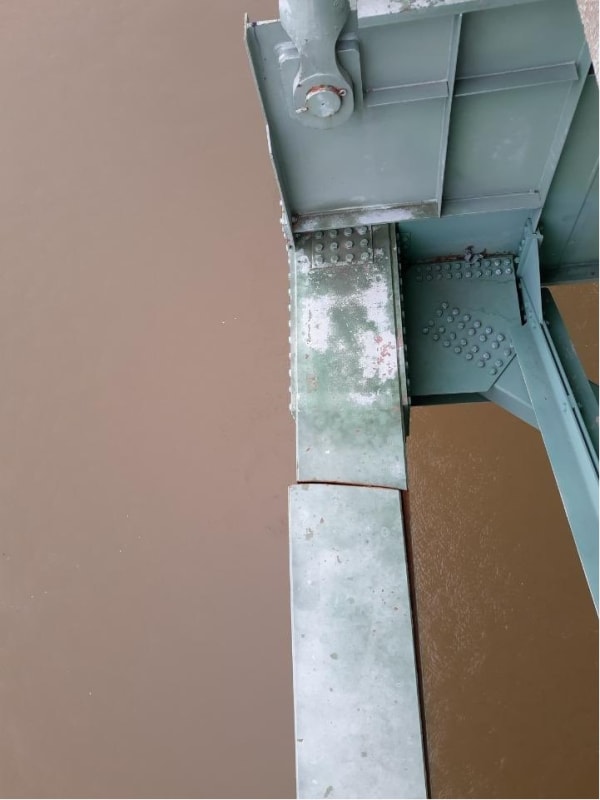
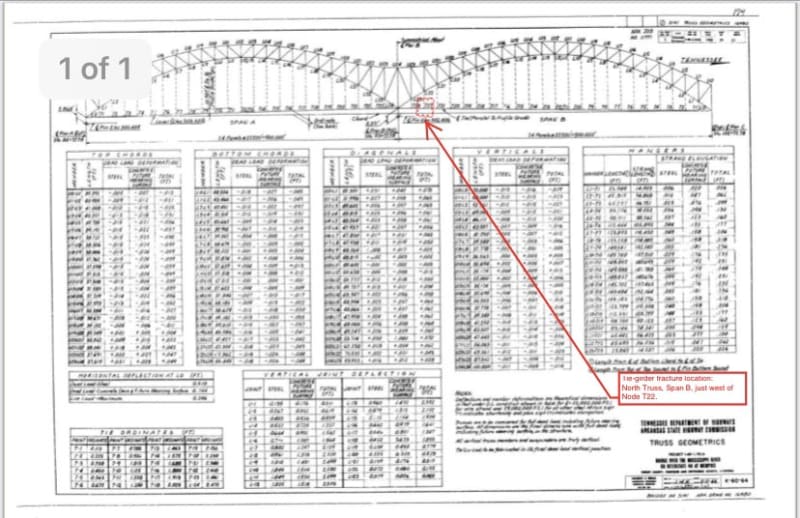
Follow along with the video below to see how to install our site as a web app on your home screen.
Note: This feature may not be available in some browsers.
Do we know what model of snooper truck was used and if the truck had enough lateral reach to operate outboard?The snooper bucket launches from the bridge deck and then articulates outboard
Sounds like possible inadequate training. Maybe a failure to properly use the axle locks.He said if you took the basket outside of the tie girder to move along the outside, the A-75 was unstable. He also said that he once moved it out there, and one of the tires lifted off the ground.
To clarify the reasons for Frazier’s firing, The Daily Memphian and Arkansas Nonprofit News Network relayed a series of questions to ArDOT’s public information officer, Dave Parker. In response to a specific question about Frazier’s termination, Parker responded that, “we have verified that Monty Frazier was the only inspector of the tie girder that was cracked between 2016 and 2020.” In a follow-up call on the evening of July 20, ArDOT’s Director, Lori Tudor, emphasized this point: “Monty Frazier was the only inspector who looked at that particular tie girder.”
This contention is contradicted by years of inspection reports provided to The Daily Memphian and ANNN. The ArDOT inspection reports include a description of each structural element of the bridge, identified by number. The tie girders on the DeSoto Bridge correspond to element #107, “Steel Open Girder/Beam.” At least five inspectors are listed as having inspected the bridge during that time. Monty Frazier is only one of them.
Another photo shows the same crack in an image dated Oct. 24, 2014. The photo is from a French tourist, Philipe Suissa, who traveled to Memphis for two days in October 2014, during a road trip from New Orleans to Chicago. “We had a boat trip and I took the photo,” he said in an email to The Daily Memphian. Metadata analysis by The Daily Memphian confirmed the date of Suissa’s photo.
Frazier has been on staff at ArDOT since 2006, but didn’t participate in DeSoto inspections until 2016. DeSoto Bridge inspections have gone through multiple lead bridge inspectors — and dozens of inspectors — since 2014.
That's a valid point Tug.TugBoatEng said:With all of that extra weight from the repairs are they going to have to reduce the capacity of the bridge?