-
1
- #161
hpaircraft
Member
This might be a silly question, but:
When I'm designing a fiberglass or carbon fiber structure, I tailor the local lamination schedule, particularly the fiber orientation, to accommodate local loads. Specifically, I use bias (usually +/-45-degree) fibers to distribute shear stresses into the rest of the structure. Based on that practice, I would have expected to see a set of angled "chevron" rebar reinforcements in the deck as shown below to distribute the thrust applied by #11 into the rest of the deck. The chevrons could go under or over the PT tendons, or maybe both.
Would that have been an unworkable approach? The argument might be made that the deck is too shallow to accommodate these, but that might just be another way of saying the deck is too shallow to function properly.
--Bob K.
When I'm designing a fiberglass or carbon fiber structure, I tailor the local lamination schedule, particularly the fiber orientation, to accommodate local loads. Specifically, I use bias (usually +/-45-degree) fibers to distribute shear stresses into the rest of the structure. Based on that practice, I would have expected to see a set of angled "chevron" rebar reinforcements in the deck as shown below to distribute the thrust applied by #11 into the rest of the deck. The chevrons could go under or over the PT tendons, or maybe both.
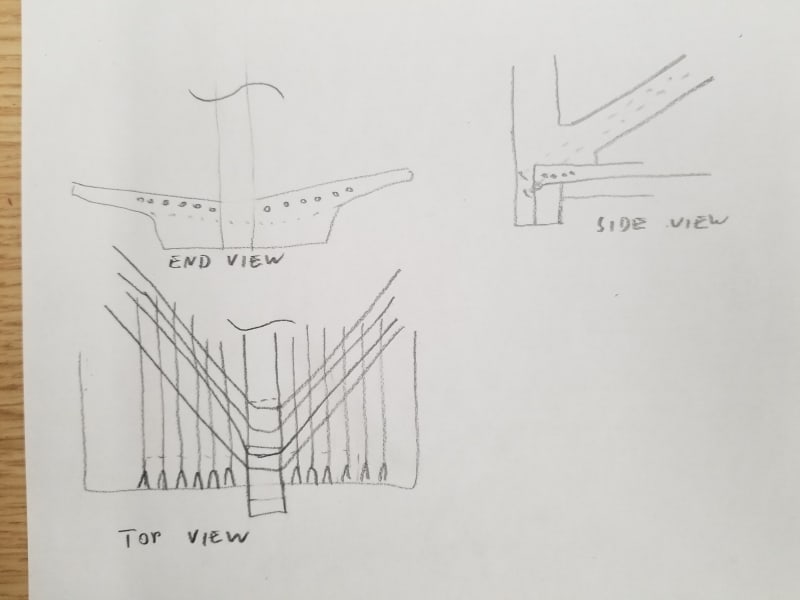
Would that have been an unworkable approach? The argument might be made that the deck is too shallow to accommodate these, but that might just be another way of saying the deck is too shallow to function properly.
--Bob K.