Andera
Mechanical
- Jan 21, 2019
- 58
I got the following explanation seen below, but I would like to ask if you agree with the assessment? I see here are many GD&T experts that can help me with my follow up questions.
Unfortunately, the discussion I had, has been deleted on the original site, as the people there (original creators) I assume were not happy with the additional questions I’ve been asking them.
The second example is a refinement of Rule #1. As such, it would be inappropriate to have a basic dimension on the size.
If you are not familiar with the hierarchy of GD&T, Profile of a Surface, with a datum reference, can locate &/or orient a feature wrt the datums. Without a datum reference, if the feature is an enclosed boundary, then it will control size and orientation of the feature. If the size is already controlled, and a profile of a surface control is applied without a datum reference, it controls the form of the feature.
In the second example, what is being controlled is co-cylindricity of the 8 surfaces. The only geometric control that locates surfaces is .... profile of a surface.
If you're not familiar with the hierarchy, it's a good time to look at GD&T from that perspective.
I would like to see update the graphic to include a composite profile control as another option
Unfortunately, the discussion I had, has been deleted on the original site, as the people there (original creators) I assume were not happy with the additional questions I’ve been asking them.
The second example is a refinement of Rule #1. As such, it would be inappropriate to have a basic dimension on the size.
If you are not familiar with the hierarchy of GD&T, Profile of a Surface, with a datum reference, can locate &/or orient a feature wrt the datums. Without a datum reference, if the feature is an enclosed boundary, then it will control size and orientation of the feature. If the size is already controlled, and a profile of a surface control is applied without a datum reference, it controls the form of the feature.
In the second example, what is being controlled is co-cylindricity of the 8 surfaces. The only geometric control that locates surfaces is .... profile of a surface.
If you're not familiar with the hierarchy, it's a good time to look at GD&T from that perspective.
I would like to see update the graphic to include a composite profile control as another option
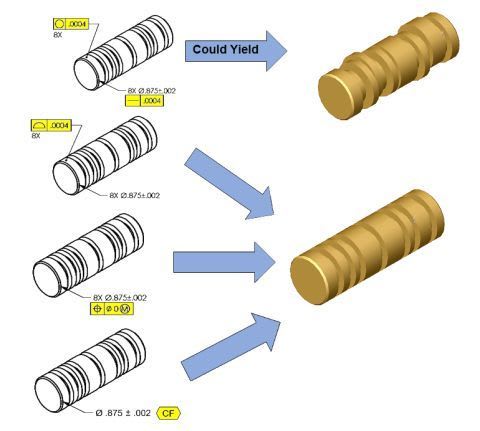