Th.Ro.
Mechanical
- Apr 2, 2019
- 23
ASME Y14.5-2009 has this for Two Coaxial Datum Features defining a Single Datum Axis:
Would it be OK to use this also with 2 sets of parallel planes like this:

Would it be OK to use this also with 2 sets of parallel planes like this:
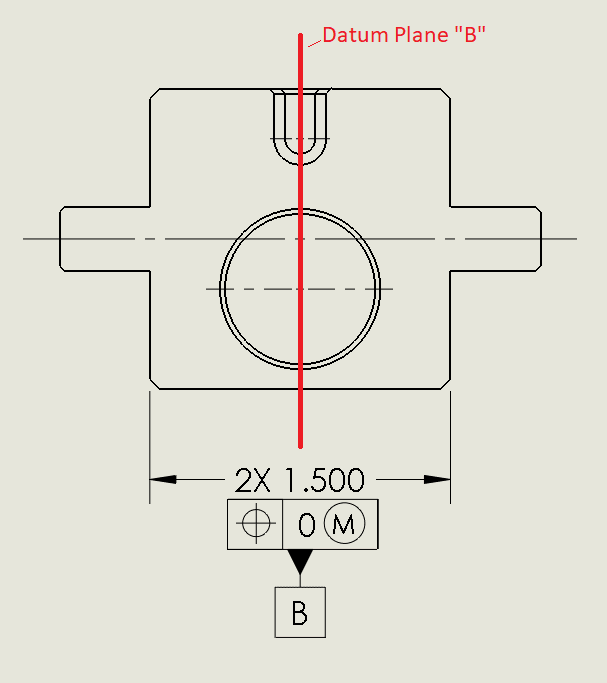