I was looking at one of our drawings and we have a drawing for a timing pulley that requires the centerplane of a particular tooth to be aligned to the centerplane of a keyway within 0.5 degrees. Currently, the requirement is that the centerplane of the tooth is aligned to the keyway and not the surface of the tooth. I assume this is because the tooth form and size are controlled by the selected profile for the timing pulley.
The tooth profile is AT10. Therefore, there are no opposing planes that can be used to derive a centerplane. Is there an established way to determine the plane, or is the dimensioning approach flawed?
Best approximation of the requirement:
The tooth profile is AT10. Therefore, there are no opposing planes that can be used to derive a centerplane. Is there an established way to determine the plane, or is the dimensioning approach flawed?
Best approximation of the requirement:
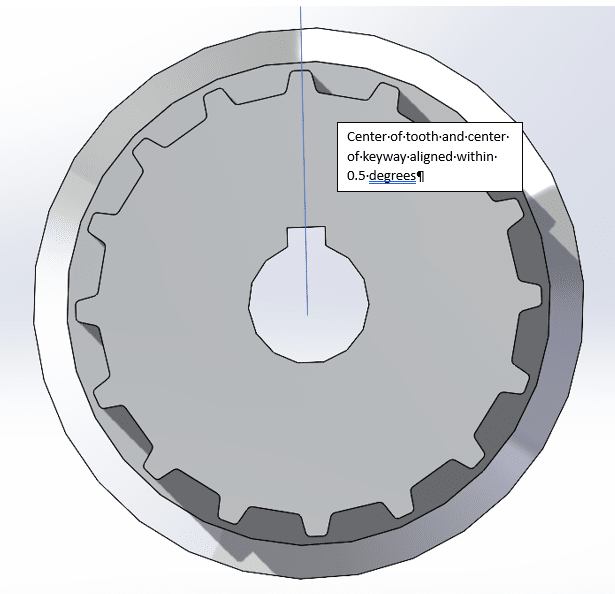