PtoMonty
Mechanical
- Sep 17, 2024
- 9
Hello all,
I have been trying to find an answer to this one and maybe you could give me your 2 cents. If I want to control the position of one hole in relation to another do you considered that I still need the 3 datums? Below I made a simplified drawing of what I consider to be a correct position tolerance for the hole in the top rigth. Am I till controlling all degrees of freedom? A is not in the picture but consider it as the plane defined by one of the faces perpendicular to the hole axis.
Thanks in advance.
I have been trying to find an answer to this one and maybe you could give me your 2 cents. If I want to control the position of one hole in relation to another do you considered that I still need the 3 datums? Below I made a simplified drawing of what I consider to be a correct position tolerance for the hole in the top rigth. Am I till controlling all degrees of freedom? A is not in the picture but consider it as the plane defined by one of the faces perpendicular to the hole axis.
Thanks in advance.
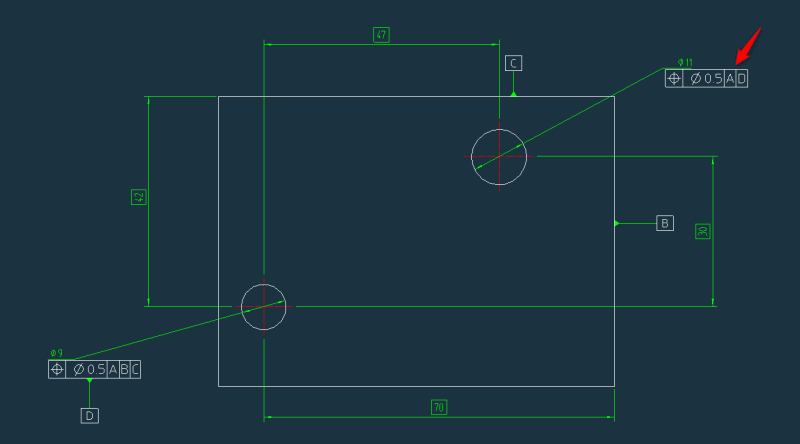