ApexM0Eng
Computer
- Feb 23, 2015
- 39
I would like to start integrating some GD&T tolerances into drawings, and I figured I would start with symmetry and true positioning
for features that I do often.
One concept I am trying to figure out is how to specify a hole should be centered within the width of a part.
Here the width is not a critical dimension, but whatever it ends up being I want the hole to be centered
with it within 5 thou of the center line.
So I mocked this up:
But from researching symmetry positioning, this doesn't seem like the proper use. What would be the right
way to specify what I wanted?
for features that I do often.
One concept I am trying to figure out is how to specify a hole should be centered within the width of a part.
Here the width is not a critical dimension, but whatever it ends up being I want the hole to be centered
with it within 5 thou of the center line.
So I mocked this up:
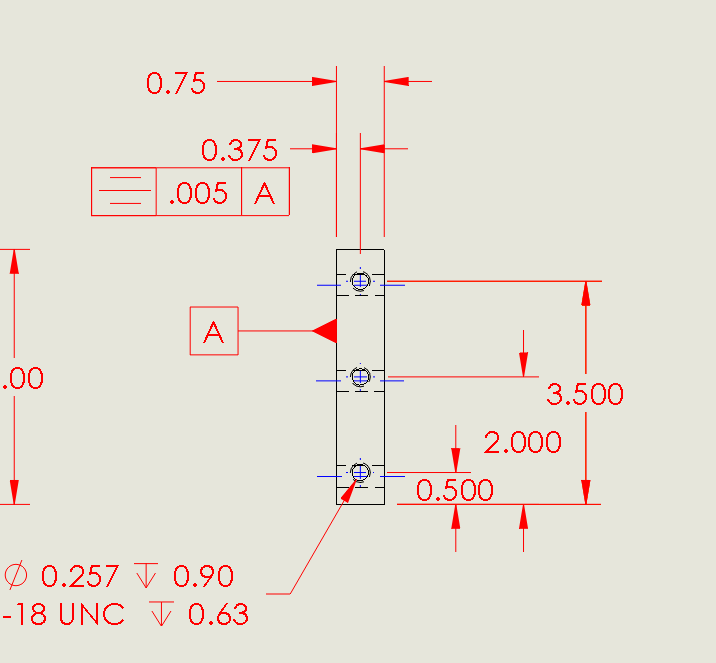
But from researching symmetry positioning, this doesn't seem like the proper use. What would be the right
way to specify what I wanted?