-
1
- #1
human909
Structural
- Mar 19, 2018
- 2,126
Some pretty serious looking issues here.
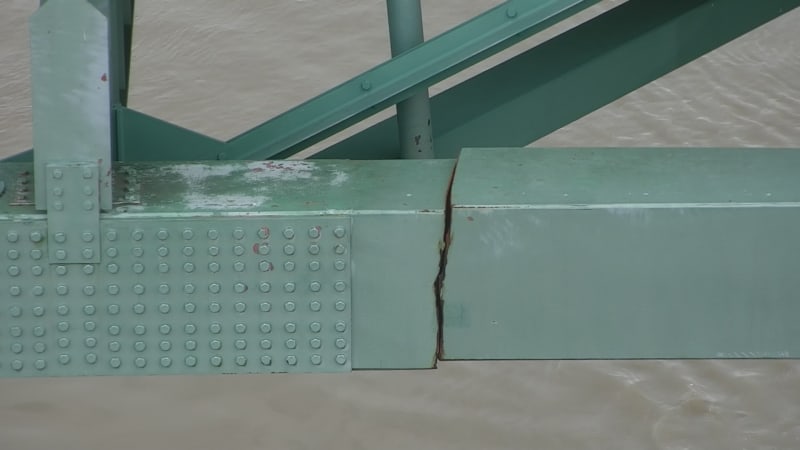
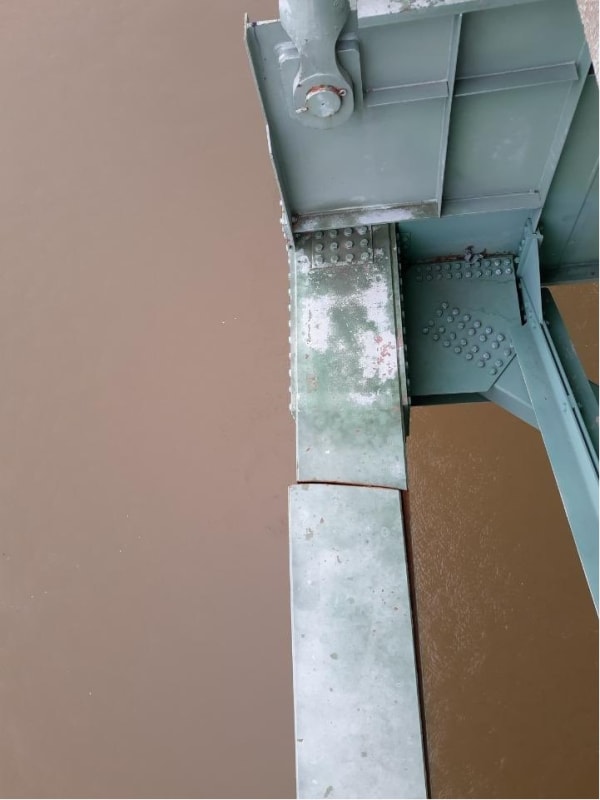
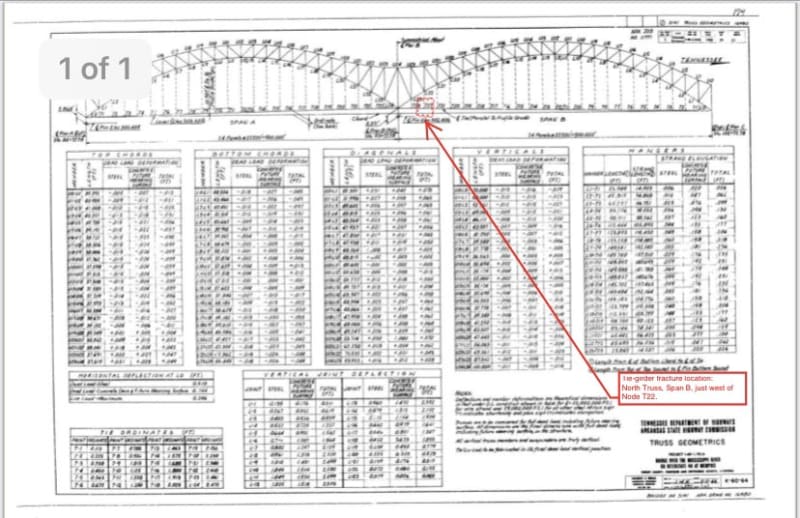
Follow along with the video below to see how to install our site as a web app on your home screen.
Note: This feature may not be available in some browsers.